A kind of linear multi-block copolymerized silicone oil and preparation method thereof
A technology of block copolymerization and silicone oil, which is applied in fiber treatment, textiles and papermaking, and improved hand-feeling fibers, etc., to achieve excellent moisture permeability, smooth air permeability, and easy reaction process
- Summary
- Abstract
- Description
- Claims
- Application Information
AI Technical Summary
Problems solved by technology
Method used
Image
Examples
Embodiment 1
[0054] (1) Put 900g (15mol) of ethylenediamine and 831g (5mol) of terephthalic acid into the reaction bottle, slowly raise the temperature to 120°C and react for 4 hours, then gradually raise the temperature to 180°C, and evaporate excess ethylenediamine and water ;
[0055] (2) Add 1500 g (5 mol) of 12-hydroxystearic acid to the polyamide prepared in the above (1), gradually raise the temperature to 200° C., and react for 15 hours;
[0056] (3) Add double-end epoxy polyether silicone oil (m=0, n=0, z=70) 13.3kg, ethylene glycol monobutyl ether 10.6kg in the polyester polyamide that above-mentioned (2) makes, Raise the temperature to 85°C and react for 16 hours to obtain 26.6 kg of linear multi-block copolymerized silicone oil containing polyester, polyamide, polyether, amino, and hydroxyl functional groups, with a volatile content of 60.2%.
Embodiment 2
[0058] (1) Put 324.42g (3mol) of p-phenylenediamine and 204.18g (2mol) of succinic acid into the reaction bottle, slowly raise the temperature to 180°C, and react for 8 hours to obtain polyamide;
[0059] Put 624.6g (3mol) of β-hydroxybutyric acid into another reaction flask, raise the temperature to 220°C, cool down after receiving about 36g of water, and obtain polyester;
[0060] (2) Mix the polyamide and polyester prepared in the above (1), heat up to 180° C. and react for 10 hours to obtain polyester polyamide;
[0061] (3) Add 3658.2 g of double-ended epoxy polyether silicone oil (m=8, n=0, z=83) and 11 kg of isopropanol to the polyester polyamide prepared in the above (2), and heat up to 80° C. After reacting for 6 hours, 7800 g of isopropanol was evaporated to obtain 7860 g of linear multi-block copolymerized silicone oil containing polyester, polyamide, polyether, amino and hydroxyl functional groups, with a solid content of 58.7%.
Embodiment 3
[0063] (1) Put 581g (5mol) of hexamethylenediamine and 584.56g (4mol) of adipic acid into the reaction bottle, slowly raise the temperature to 180°C, and react for 10h to prepare polyamide;
[0064] Put 450.4g (5mol) of L-lactic acid (5mol) and 300ml of n-hexane into the reaction flask, heat up to reflux for dehydration, and when the amount of water is removed to about 72ml, distill out the n-hexane to obtain lactic acid polyester;
[0065] (2) Mix the polyamide and lactic acid polyester prepared in the above (1), heat up to 180° C., and react for 8 hours to obtain polyester polyamide;
[0066] (3) Add double-end epoxy polyether silicone oil (m=18, n=13, z=200) 8760g, isopropoxyethanol 10.16kg in the polyester polyamide that above-mentioned (2) makes, heat up to React at 120°C for 4 hours to obtain 20.3 kg of linear multi-block copolymer silicone oil containing polyester, polyamide, polyether, amino, and hydroxyl functional groups, with a solid content of 50.2%.
[0067] The ...
PUM
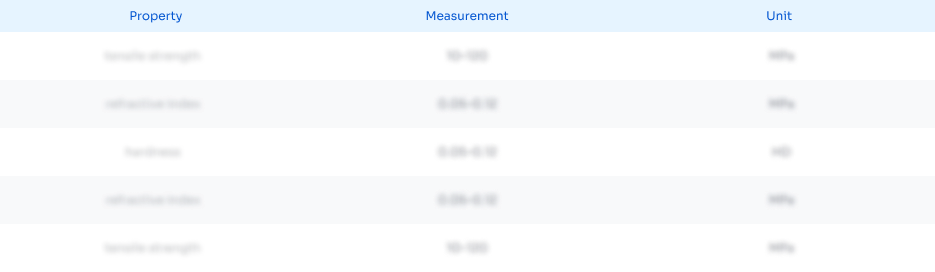
Abstract
Description
Claims
Application Information

- R&D Engineer
- R&D Manager
- IP Professional
- Industry Leading Data Capabilities
- Powerful AI technology
- Patent DNA Extraction
Browse by: Latest US Patents, China's latest patents, Technical Efficacy Thesaurus, Application Domain, Technology Topic, Popular Technical Reports.
© 2024 PatSnap. All rights reserved.Legal|Privacy policy|Modern Slavery Act Transparency Statement|Sitemap|About US| Contact US: help@patsnap.com