Preparation method of high-toughness non-magnetic Ti(C,N)-based metal ceramic
A technology of high strength and toughness and base metal, applied in the field of powder metallurgy, can solve the problems of reducing the toughness of materials, and achieve the effect of improving toughness, increasing activity, and enhancing interface bonding strength
- Summary
- Abstract
- Description
- Claims
- Application Information
AI Technical Summary
Problems solved by technology
Method used
Examples
Embodiment 1
[0033] 1. Preparation of intermediate reaction products: TiO 2 Powder, W powder and activated carbon powder are raw materials, and according to Table 1, prepare 4 kinds of intermediate reaction product powders with different components and place them in a planetary ball mill for high-energy ball milling. reaction product;
[0034] 2 Ball milling mixture: the intermediate reaction product obtained in step 1, TiN powder, Ni powder, Mo powder, Ti 2 AlN powder and AlN powder were used as raw materials, and 4 kinds of mixtures with different components were prepared according to Table 2, and placed in a planetary ball mill for ball milling and uniform mixing. The ball mill speed was 260 rpm, the ball-to-material ratio was 5:1, and the time was 36 hours;
[0035] 3. Add molding agent: the molding agent uses polyvinyl alcohol aqueous solution with a concentration of 7wt.%, and the addition ratio is 3wt% of the mixture;
[0036] 4 Compression molding: compression molding under 150MP...
Embodiment 2
[0043] 1. Preparation of intermediate reaction products: TiO 2 Powder, W powder and activated carbon powder are raw materials, according to Table 1, prepare 4 kinds of intermediate reaction product powders with different components and place them in a planetary ball mill for high-energy ball milling. reaction product;
[0044] 2 Ball milling mixture: the intermediate reaction product obtained in step 1, TiN powder, Ni powder, Mo powder, Ti 2 AlN powder and AlN powder were used as raw materials, and 4 kinds of mixtures with different components were prepared according to Table 2, and placed in a planetary ball mill for ball milling and uniform mixing. The ball mill speed was 400rpm, the ball-to-material ratio was 5:1, and the time was 24h;
[0045] 3. Add molding agent: the molding agent uses polyvinyl alcohol aqueous solution with a concentration of 7wt.%, and the addition ratio is 6wt% of the mixture;
[0046] 4 Compression molding: compression molding under 200MPa pressure...
Embodiment 3
[0053] 1. Preparation of intermediate reaction products: TiO 2 powder, W powder and activated carbon powder as raw materials, according to Table 1, prepare 4 kinds of intermediate reaction product powders with different components and place them in a planetary ball mill for high-energy ball milling. reaction product;
[0054] 2 Ball milling mixture: the intermediate reaction product obtained in step 1, TiN powder, Ni powder, Mo powder, Ti 2 AlN powder and AlN powder were used as raw materials, and 4 kinds of mixtures with different components were prepared according to Table 2, and placed in a planetary ball mill for ball milling and uniform mixing.
[0055] 3. Add molding agent: the molding agent uses polyvinyl alcohol aqueous solution with a concentration of 7wt.%, and the addition ratio is 4wt% of the mixture;
[0056] 4 Compression molding: compression molding under 250MPa pressure to obtain compact;
[0057] 5 Forming agent removal: place the compact in a vacuum / atmosp...
PUM
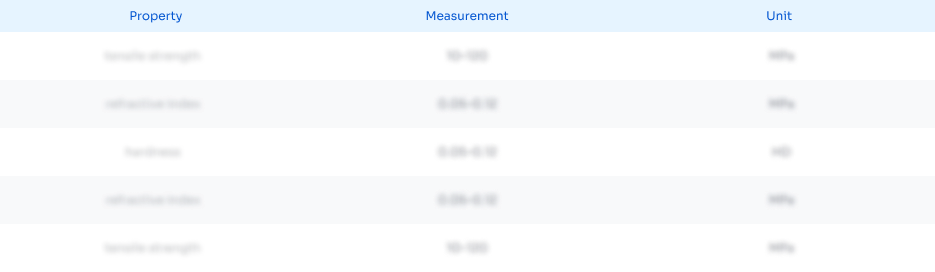
Abstract
Description
Claims
Application Information

- Generate Ideas
- Intellectual Property
- Life Sciences
- Materials
- Tech Scout
- Unparalleled Data Quality
- Higher Quality Content
- 60% Fewer Hallucinations
Browse by: Latest US Patents, China's latest patents, Technical Efficacy Thesaurus, Application Domain, Technology Topic, Popular Technical Reports.
© 2025 PatSnap. All rights reserved.Legal|Privacy policy|Modern Slavery Act Transparency Statement|Sitemap|About US| Contact US: help@patsnap.com