Method of producing sinter by using high-proportion Baiyenebo iron ore concentrate
A technology for iron concentrate and sinter, which is applied in the field of metallurgy, can solve the problems of poor air permeability of material layer, poor granulation of mixed material, influence on sintering process, etc. Effect
- Summary
- Abstract
- Description
- Claims
- Application Information
AI Technical Summary
Problems solved by technology
Method used
Image
Examples
Embodiment 1
[0037] Carry out batching according to raw material and proportioning shown in Table 2. The prepared mixture was mixed uniformly in the primary mixer, and then mixed and granulated again in the secondary mixing granulator. The granulation time was 3 minutes, and the mass percentage of water in the mixture was controlled at 7.5%. The granulated mixture is evenly distributed to 500m through the distribution device 2 On the large-scale sintering machine trolley, the thickness of the material layer is 800mm. The igniter of the sintering machine head is ignited. The ignition fuel is coke oven gas. The ignition time is 1.5min. At the same time, the bottom of the sintering machine starts to draft, forming a certain negative The ignition negative pressure is 4900Pa. After ignition, the air is sucked away through the sintering layer from top to bottom. The sintering flue gas is discharged into the atmosphere after the desulfurization process. The sintering exhaust negative pressure is ...
Embodiment 2
[0039] Carry out batching according to raw material and proportioning shown in Table 2. The prepared mixture was mixed uniformly in the primary mixer, and then mixed and granulated again in the secondary mixing granulator. The granulation time was 5 minutes, and the mass percentage of water in the mixture was controlled at 7.8%. The granulated mixture is evenly distributed to 500m through the distribution device 2 On the large-scale sintering machine trolley, the thickness of the material layer is 800mm. The igniter of the sintering machine head is ignited. The ignition fuel is coke oven gas. The ignition time is 2.0min. At the same time, the bottom of the sintering machine starts to draw air, forming a certain negative The ignition negative pressure is 5900Pa. After ignition, the air is sucked away through the sintering material layer from top to bottom. The sintering flue gas is discharged into the atmosphere after the desulfurization process. The sintering exhaust negative ...
PUM
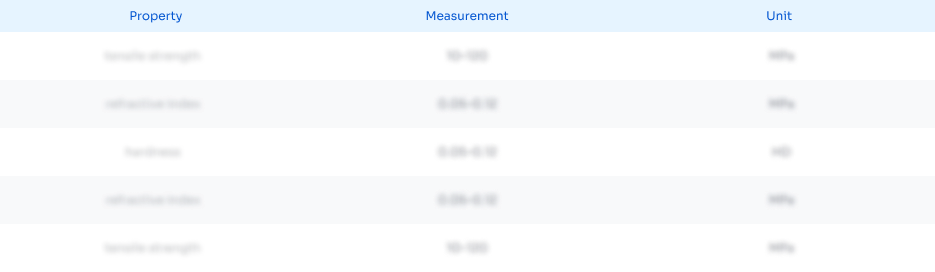
Abstract
Description
Claims
Application Information

- R&D
- Intellectual Property
- Life Sciences
- Materials
- Tech Scout
- Unparalleled Data Quality
- Higher Quality Content
- 60% Fewer Hallucinations
Browse by: Latest US Patents, China's latest patents, Technical Efficacy Thesaurus, Application Domain, Technology Topic, Popular Technical Reports.
© 2025 PatSnap. All rights reserved.Legal|Privacy policy|Modern Slavery Act Transparency Statement|Sitemap|About US| Contact US: help@patsnap.com