Combined electrode structure of space solar cell array conductor resistance welding
A solar cell array and wire resistance technology, applied in the direction of resistance electrode base, electrode characteristics, etc., can solve the problems of inability to clamp welding objects in pairs, constraints, and difficulty in process control, so as to achieve the convenience of welding process implementation and the smoothness of solder joints. Reliable, stable welding performance results
- Summary
- Abstract
- Description
- Claims
- Application Information
AI Technical Summary
Problems solved by technology
Method used
Image
Examples
Embodiment Construction
[0011] In order to make the content of the present invention more clearly understood, the present invention will be further described in detail below based on specific embodiments and in conjunction with the accompanying drawings.
[0012] Such as figure 1 As shown, an electrode structure for resistance welding of space solar array wires includes a positive electrode pressure welding part 1 , a negative electrode pressure welding part 2 , and a negative electrode clamping backing plate 3 .
[0013] In order to avoid explosion welding during the welding process, the positive electrode pressure welding part 1 and the negative electrode pressure welding part 2 are made of pure molybdenum material, and the negative electrode clamping backing plate 3 is made of brass material.
[0014] The working principle of the present invention is as follows: the combined welding electrode of the present invention is composed of three parts; during welding, the positive electrode pressure weldi...
PUM
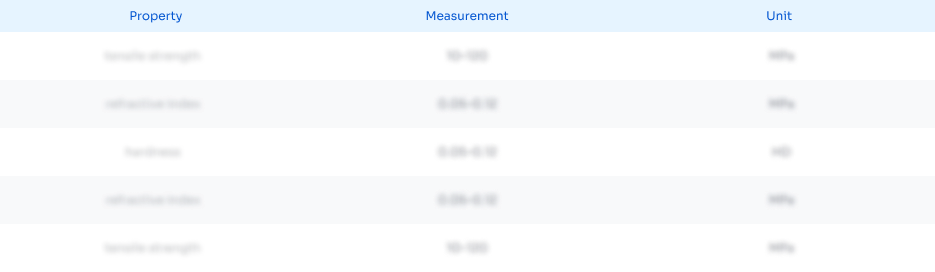
Abstract
Description
Claims
Application Information

- R&D
- Intellectual Property
- Life Sciences
- Materials
- Tech Scout
- Unparalleled Data Quality
- Higher Quality Content
- 60% Fewer Hallucinations
Browse by: Latest US Patents, China's latest patents, Technical Efficacy Thesaurus, Application Domain, Technology Topic, Popular Technical Reports.
© 2025 PatSnap. All rights reserved.Legal|Privacy policy|Modern Slavery Act Transparency Statement|Sitemap|About US| Contact US: help@patsnap.com