Screw extrusion-kettle type stirred combined reactor and application thereof
A technology of screw extrusion and screw extruder, which is applied in the field of screw extrusion-kettle type mixing combined reactor, which can solve the problems of production difficulty and pipeline transmission resistance, and achieve low cost, simple equipment manufacturing and continuous production Effect
- Summary
- Abstract
- Description
- Claims
- Application Information
AI Technical Summary
Problems solved by technology
Method used
Image
Examples
Embodiment 1
[0033] A screw extruder-tank type stirring combined reactor, comprising a reactor 1, a first screw extruder 2 and a second screw extruder 3; the first screw extruder 2 and the reactor 1 The feed port is connected, and the second screw extruder 3 is connected with the discharge port of the reactor 1;
[0034] Described reactor 1 is provided with stirring motor 5, and described stirring motor 5 is provided with stirring shaft 6, and described stirring shaft 6 is provided with stirring blade 7; The bottom of described reactor 1 is provided with conveying screw rod 4, The conveying screw 4 is connected with the stirring shaft 6 so that the stirring shaft 6 rotates to drive the conveying screw 4 to rotate;
[0035] The first screw extruder 2 is provided with a main material feeding port 11, and the second screw extruder 3 is provided with a vacuum pump 12;
[0036] The reactor 1 is a reactor composed of an upright steel cylinder and an upper and lower arc-shaped head. The height-t...
Embodiment 2
[0042] A screw extruder-tank type stirring combined reactor, comprising a reactor 1, a first screw extruder 2 and a second screw extruder 3; the first screw extruder 2 and the reactor 1 The feed port is connected, and the second screw extruder 3 is connected with the discharge port of the reactor 1;
[0043] Described reactor 1 is provided with stirring motor 5, and described stirring motor 5 is provided with stirring shaft 6, and described stirring shaft 6 is provided with stirring blade 7; The bottom of described reactor 1 is provided with conveying screw rod 4, The conveying screw 4 is connected with the stirring shaft 6 so that the stirring shaft 6 rotates to drive the conveying screw 4 to rotate;
[0044] The first screw extruder 2 is provided with a main material feeding port 11, and the second screw extruder 3 is provided with a vacuum pump 12;
[0045] The reactor 1 is a reactor composed of an upright steel cylinder and an upper and lower arc-shaped head. The height-t...
PUM
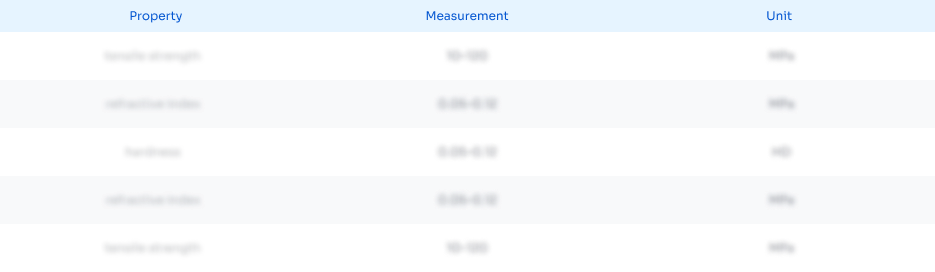
Abstract
Description
Claims
Application Information

- R&D Engineer
- R&D Manager
- IP Professional
- Industry Leading Data Capabilities
- Powerful AI technology
- Patent DNA Extraction
Browse by: Latest US Patents, China's latest patents, Technical Efficacy Thesaurus, Application Domain, Technology Topic, Popular Technical Reports.
© 2024 PatSnap. All rights reserved.Legal|Privacy policy|Modern Slavery Act Transparency Statement|Sitemap|About US| Contact US: help@patsnap.com