High-power high-stability variable-load high-frequency acceleration system
A high-stability, acceleration system technology, applied in the direction of magnetic resonance accelerators, accelerators, electrical components, etc., can solve problems such as the coupling degree cannot be automatically adjusted, and achieve the effects of convenient debugging, compact structure, and high data bandwidth
- Summary
- Abstract
- Description
- Claims
- Application Information
AI Technical Summary
Problems solved by technology
Method used
Image
Examples
Embodiment Construction
[0042] 1. Basic structure of high-energy circular accelerator. Such as figure 1 As shown, a circular accelerator is generally composed of a plurality of magnet assemblies 1 that periodically generate twisted orbits and a high-frequency cavity 2 , and the high-frequency cavity 2 is arranged in a long drift section 3 between the magnet assemblies 1 . The energy-injected particles 4 enter the inner orbit of the accelerator, perform spiral motion under the magnet deflection of the magnet assembly 1, continuously obtain energy gain through the high-frequency cavity, and finally move to the outer orbit of the accelerator to extract energy. It is to draw energy particles 5 .
[0043] 2. The problem to be solved by the present invention. The invention solves the problem of how to ensure the stability of the high-frequency system under the condition of high power and variable load. Under high power conditions, when the required accelerating voltage is established, the low Q value ca...
PUM
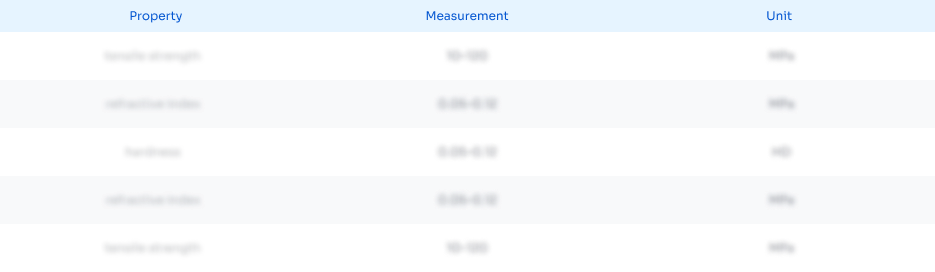
Abstract
Description
Claims
Application Information

- R&D
- Intellectual Property
- Life Sciences
- Materials
- Tech Scout
- Unparalleled Data Quality
- Higher Quality Content
- 60% Fewer Hallucinations
Browse by: Latest US Patents, China's latest patents, Technical Efficacy Thesaurus, Application Domain, Technology Topic, Popular Technical Reports.
© 2025 PatSnap. All rights reserved.Legal|Privacy policy|Modern Slavery Act Transparency Statement|Sitemap|About US| Contact US: help@patsnap.com