A kind of preparation method of ultra-low quantitative regenerated cellulose fiber screen
A technology of regenerated cellulose and fiber mesh, which is applied in the direction of single-component cellulose rayon, complete sets of equipment for the production of rayon, rayon manufacturing, etc. Deterioration of performance, aggravation of silk aging and deterioration, etc., to achieve the effects of large-scale continuous production, improved uniformity, and simple and easy-to-control spinning process
- Summary
- Abstract
- Description
- Claims
- Application Information
AI Technical Summary
Problems solved by technology
Method used
Image
Examples
Embodiment 1
[0030] As shown in Figure 1, the production equipment consists of a dissolution kettle 1, a screw extruder 2, a metering pump 3, an air flow 4, a spinning die head 5, a guide roller 6, a primary desolvent spraying device 7, a collection roller 8 and The deep desolvation pool consists of 9 components. After mixing the nano-magnesium oxide, nano-titanium dioxide, nano-zinc oxide and cellulose / N-methylmorpholine oxide slurry through the dissolution kettle 1, the screw extruder 2 controls the supply of the slurry through the metering pump 3, and the The slurry is sprayed out from the spinning die 5, and then blown to the guide roller 6 by the air flow 4, and the N-methylmorpholine oxide solvent in the guide roller and the screen is subjected to primary desolvation treatment, and then sent to the reciprocating machine capable of continuously collecting fibers. On the type swing collection roller 8, the ultra-low weight regenerated cellulose fiber web for paper repair is formed thro...
Embodiment 2
[0034] Using the production equipment described in Example 1, mix the mass fraction of 6% cellulose with N-methylmorpholine oxide solution, and add it to the dissolution kettle for stirring. During the stirring process, dehydration under reduced pressure is continued, and the dissolution temperature is always maintained. At 80-100°C, after the stirring is completed, a uniformly dispersed N-methylmorpholine oxide solution with a cellulose content of 3% is obtained.
[0035] Mix nano-magnesia with a mass fraction of 0.4%, nano-titanium dioxide with a mass fraction of 0.3%, and nano-zinc oxide with a mass fraction of 0.1% into an N-methylmorpholine oxide solution with a cellulose content of 3%. For thread extrusion, the temperature of the die head is controlled at 120°C during extrusion, the pump supply rate of the spinneret hole of the die head is 0.06g / min per hole, the pressure inside the die head is 0.2MPa, and the temperature is 130°C Compressed air, The fibers are blown ont...
Embodiment 3
[0037] Using the production equipment described in Example 1, mix 4% cellulose by mass fraction with N-methylmorpholine oxide solution, and add it to the dissolution kettle for stirring. During the stirring process, dehydration under reduced pressure is continued, and the dissolution temperature is always maintained. At 80-100°C, after the stirring is completed, a uniformly dispersed N-methylmorpholine oxide solution with a cellulose content of 2% is obtained.
[0038] Mix nano-magnesia with a mass fraction of 0.1%, nano-titanium dioxide with a mass fraction of 0.2%, and nano-zinc oxide with a mass fraction of 0.3% into an N-methylmorpholine oxide solution with a cellulose content of 2%. For thread extrusion, the temperature of the die head is controlled at 120°C during extrusion, the pump supply rate of the spinneret hole of the die head is 0.003g / min per hole, the internal pressure of the die head is 0.5MPa, and the temperature is 140°C Compressed air, The fibers were blown ...
PUM
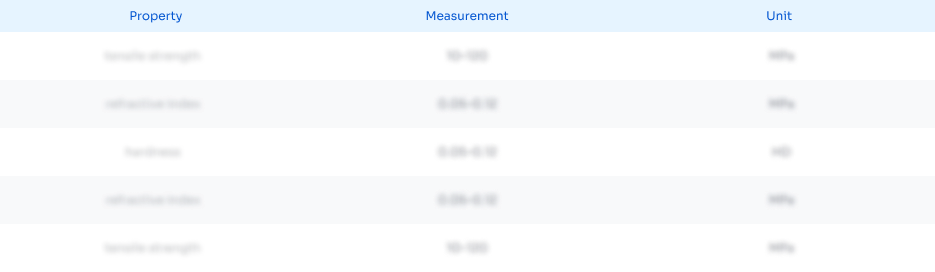
Abstract
Description
Claims
Application Information

- R&D
- Intellectual Property
- Life Sciences
- Materials
- Tech Scout
- Unparalleled Data Quality
- Higher Quality Content
- 60% Fewer Hallucinations
Browse by: Latest US Patents, China's latest patents, Technical Efficacy Thesaurus, Application Domain, Technology Topic, Popular Technical Reports.
© 2025 PatSnap. All rights reserved.Legal|Privacy policy|Modern Slavery Act Transparency Statement|Sitemap|About US| Contact US: help@patsnap.com