Manufacturing method for skeleton-free niobium-tri-tin superconducting coil
A technology for superconducting coils and manufacturing methods, applied in coil manufacturing, inductance/transformer/magnet manufacturing, electrical components, etc., capable of solving problems such as deformation of niobium-three-tin superconducting coils and reduction of total current density of niobium-three-tin superconducting coils , to achieve superior electrical insulation performance, excellent thermal stability, and reduce cooling capacity
- Summary
- Abstract
- Description
- Claims
- Application Information
AI Technical Summary
Problems solved by technology
Method used
Image
Examples
Embodiment 1
[0035] Connect the cylindrical quartz tube 1 to the two-end plate flange 2, open a circular groove at the junction of the two-end plate flange 2 and the cylindrical quartz tube 1, and insert the cylindrical quartz tube 1 into the circular groove 10 . There is a through hole in the center of the flange 2 of the two end plates, and an M6 screw rod 6 is installed in the through hole. The flanges 2 of the two end plates are tangent to the inner surface of the cylindrical quartz tube 1 and each has a circle of through holes in the circumferential direction, and the number of through holes is three. Three through holes are installed with three M4 screw rods 7 for positioning and clamping, so that the center of the cylindrical quartz tube 1 and the flanges 2 of the end plates are aligned and tightly connected. Install the assembled quartz skeleton on the winding machine. Two layers of glass cloth 3 are wound around the outer surface of the cylindrical quartz tube in half. The wire...
Embodiment 2
[0038] The cylindrical quartz tube 4 is connected with the flanges 2 of the two ends through the annular grooves 10 on the flanges 2 of the two ends. Install a screw rod 6 at the flange center of the two end plates, and fix it with nuts at both ends. There is a through hole in the flange center of the two end plates, and an M20 screw rod 7 is installed in the through hole. The two end plates 2 and the inner surface of the cylindrical quartz tube 1 are respectively provided with a circle of through holes in the circumferential direction, and the number of the through holes is 6. Six M4 screw rods 7 are installed in the through holes for positioning and clamping, so that the center of the cylindrical quartz tube 1 and the flanges 2 of the end plates are aligned and tightly connected. Install the assembled quartz skeleton on the winding machine. Two layers of glass cloth 3 are wound around the outer surface of the cylindrical quartz tube in half. The wires are fed into the wir...
PUM
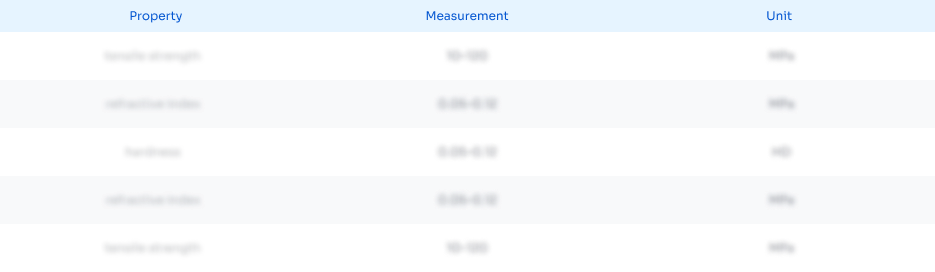
Abstract
Description
Claims
Application Information

- R&D
- Intellectual Property
- Life Sciences
- Materials
- Tech Scout
- Unparalleled Data Quality
- Higher Quality Content
- 60% Fewer Hallucinations
Browse by: Latest US Patents, China's latest patents, Technical Efficacy Thesaurus, Application Domain, Technology Topic, Popular Technical Reports.
© 2025 PatSnap. All rights reserved.Legal|Privacy policy|Modern Slavery Act Transparency Statement|Sitemap|About US| Contact US: help@patsnap.com