Absolute anti-aliasing multi-scale filtering method for rotary mechanical structure complex harmonic dynamic process
A technology of rotating machinery and dynamic process, applied in the testing of machine/structural components, measurement of ultrasonic/sonic/infrasonic waves, measurement devices, etc., can solve problems such as distortion of decomposition results that cannot be overcome, and achieve elimination of energy aliasing sources and regularization. The effect of good performance and good engineering application promotion value
- Summary
- Abstract
- Description
- Claims
- Application Information
AI Technical Summary
Problems solved by technology
Method used
Image
Examples
Embodiment Construction
[0039] The content of the present invention will be described in further detail below in conjunction with the accompanying drawings.
[0040] The present invention comprises the following steps:
[0041] 1. Install a non-contact eddy current sensor on the bearing seat of a rotating mechanical equipment operating at a constant speed to collect vibration displacement signals (such as figure 1 shown) to carry out mean value processing, to obtain x:={x(n)|n=0,2,...,N-1}, the sampling frequency of the signal is f s , the sampling length N of the signal must be an even number, and the acquisition process is processed by hardware anti-aliasing filtering, and the frequency is greater than or equal to 0.5f sThe components are suppressed, and the frequency resolution of the signal is required to be Δf=f s / N≤1Hz.
[0042] 2. Extract the frequency, amplitude and phase information of each high-energy harmonic component in the signal through the redundant Fourier transform feature, the ...
PUM
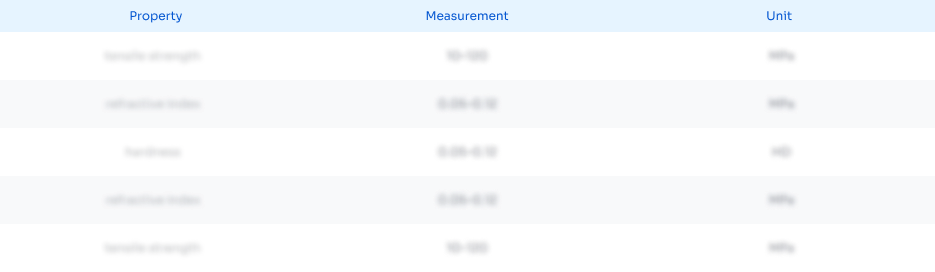
Abstract
Description
Claims
Application Information

- R&D
- Intellectual Property
- Life Sciences
- Materials
- Tech Scout
- Unparalleled Data Quality
- Higher Quality Content
- 60% Fewer Hallucinations
Browse by: Latest US Patents, China's latest patents, Technical Efficacy Thesaurus, Application Domain, Technology Topic, Popular Technical Reports.
© 2025 PatSnap. All rights reserved.Legal|Privacy policy|Modern Slavery Act Transparency Statement|Sitemap|About US| Contact US: help@patsnap.com