Construction technology for spraying wear resistant coating
A technology of wear-resistant coating and construction technology, which is applied in the direction of metal material coating technology, coating, fusion spraying, etc., can solve the problems of thin coating surface, limited wear resistance, easy to be damaged, etc., and achieve excellent durability High grinding performance and high efficiency
- Summary
- Abstract
- Description
- Claims
- Application Information
AI Technical Summary
Problems solved by technology
Method used
Examples
Embodiment 1
[0015] A construction technique for spraying wear-resistant coatings, specifically comprising the following steps:
[0016] (1) Pretreatment of the surface of metal fittings, including dust removal, rust removal, and degreasing;
[0017] (2) Surface defects of grinding parts;
[0018] (3) Abrasive the surface of the accessories to meet the roughness required by the coating;
[0019] (4) Use a spray gun to spray special wear-resistant alloy powder on the surface of the accessories as a whole. The spray distance of the spray gun is 270mm, the spray angle is 45°, and the air source pressure of the spray gun is 0.6MPa;
[0020] (5) Heat the metal fittings to remelt the wear-resistant coating. The remelting temperature is 900°C and the time is 180s;
[0021] (6) Use abrasive belts to polish metal fittings.
Embodiment 2
[0023] A construction technique for spraying wear-resistant coatings, specifically comprising the following steps:
[0024] (1) Pretreatment of the surface of metal fittings, including dust removal, rust removal, and degreasing;
[0025] (2) Surface defects of grinding parts;
[0026] (3) Abrasive the surface of the accessories to meet the roughness required by the coating;
[0027] (4) Use a spray gun to spray special wear-resistant alloy powder on the surface of the accessories as a whole. The spray distance of the spray gun is 300mm, the spray angle is 60°, and the air source pressure of the spray gun is 0.8MPa;
[0028] (5) Heat the metal fittings to remelt the wear-resistant coating. The remelting temperature is 950°C and the time is 240s;
[0029] (6) Use abrasive belts to polish metal fittings.
Embodiment 3
[0031] A construction technique for spraying wear-resistant coatings, specifically comprising the following steps:
[0032] (1) Pretreatment of the surface of metal fittings, including dust removal, rust removal, and degreasing;
[0033] (2) Surface defects of grinding parts;
[0034] (3) Abrasive the surface of the accessories to meet the roughness required by the coating;
[0035] (4) Use a spray gun to spray special wear-resistant alloy powder on the surface of the accessories as a whole. The spray distance of the spray gun is 285mm, the spray angle is 50°, and the air source pressure of the spray gun is 0.7MPa;
[0036] (5) Heat the metal fittings to remelt the wear-resistant coating. The remelting temperature is 925°C and the time is 210s;
[0037] (6) Use abrasive belts to polish metal fittings.
PUM
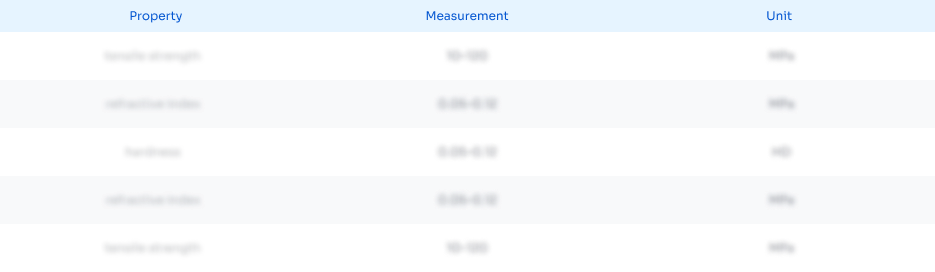
Abstract
Description
Claims
Application Information

- R&D Engineer
- R&D Manager
- IP Professional
- Industry Leading Data Capabilities
- Powerful AI technology
- Patent DNA Extraction
Browse by: Latest US Patents, China's latest patents, Technical Efficacy Thesaurus, Application Domain, Technology Topic, Popular Technical Reports.
© 2024 PatSnap. All rights reserved.Legal|Privacy policy|Modern Slavery Act Transparency Statement|Sitemap|About US| Contact US: help@patsnap.com