Forging forming method of water chamber head with side nozzle
A water chamber head and side nozzle technology, applied in the field of casting, can solve the problems of complex shape, limited stamping and forging, etc.
- Summary
- Abstract
- Description
- Claims
- Application Information
AI Technical Summary
Problems solved by technology
Method used
Image
Examples
Embodiment Construction
[0017] The invention provides a segmental profiling forming method to complete the forging forming of the water chamber head with asymmetrical side nozzles.
[0018] The first step is compaction; since the asymmetric side nozzle and the bottom of the water chamber head are integrally copied and the side nozzle is solid (such as figure 1 As shown), so the wall thickness here is thick, and the use of large steel ingots requires large deformation to break up metallurgical defects. First heat the cutting handle to reduce weight, then enter the furnace at 1150-1250°C for heat preservation, and then make JTS at the mouth of 2300mm, and then return to the furnace to heat for two upsetting and two drawing, the axial forging ratio is ≥3.
[0019] The second step is to divide the materials; there are two problems when dividing the materials:
[0020] 1. The center of the side nozzle part and the main part are different;
[0021] 2. The main part of the "bowl" shape needs to be pressed...
PUM
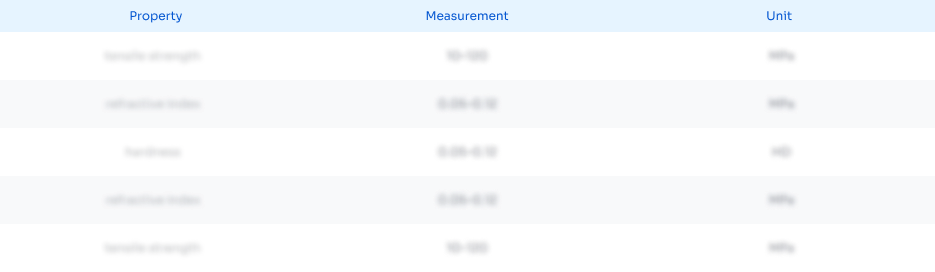
Abstract
Description
Claims
Application Information

- Generate Ideas
- Intellectual Property
- Life Sciences
- Materials
- Tech Scout
- Unparalleled Data Quality
- Higher Quality Content
- 60% Fewer Hallucinations
Browse by: Latest US Patents, China's latest patents, Technical Efficacy Thesaurus, Application Domain, Technology Topic, Popular Technical Reports.
© 2025 PatSnap. All rights reserved.Legal|Privacy policy|Modern Slavery Act Transparency Statement|Sitemap|About US| Contact US: help@patsnap.com