Preparation method of abrasion-resistant plastic package material and application thereof
A technology for plastic packaging and packaging materials, applied in the field of plastic packaging materials, can solve the problems of difficult to meet industrial production, wear resistance and strength are difficult to achieve great breakthroughs, etc., and achieve the effect of improving performance.
- Summary
- Abstract
- Description
- Claims
- Application Information
AI Technical Summary
Problems solved by technology
Method used
Examples
Embodiment 1
[0020] (1) Add 35 parts of polyethylene glycol diacrylate, 22 parts of alkyd resin, and 4 parts of nano-cerium oxide into the reaction kettle for mixing, then add the same mass of propyl acetate, stir at 70°C for 35 minutes, and the stirring speed Be 500 revs / min, obtain premix;
[0021] (2) Mix 28 parts of polyglycolic acid, 10 parts of bamboo fiber, 8 parts of vinyl bis stearamide, 3 parts of melamine polyphosphate and 200 parts of deionized water, and perform ultrasonic treatment at 400 W for 15 minutes. Obtain the ultrasonic treatment mixture, then add 6 parts of polybenzimidazole to the ultrasonic treatment mixture, raise the temperature to 65°C, keep it under nitrogen protection for 8 hours, cool to room temperature and filter after the reaction, filter the product with absolute ethanol Washing 2 to 3 times, and drying to obtain a composite reaction product;
[0022] (3) Add 55 parts of polyvinylidene chloride, 7 parts of sodium polystyrene sulfonate, 6 parts of methyl ...
Embodiment 2
[0026] (1) Add 40 parts of polyethylene glycol diacrylate, 25 parts of alkyd resin, and 5 parts of nano-cerium oxide into the reaction kettle for mixing, then add the same mass of propyl acetate, stir at 75°C for 40 minutes, and the stirring speed Be 550 revs / min, obtain premix;
[0027] (2) Mix 30 parts of polyglycolic acid, 12 parts of bamboo fiber, 10 parts of vinyl bis stearamide, 4 parts of melamine polyphosphate and 200 parts of deionized water, and perform ultrasonic treatment at 450 W for 20 minutes. Obtain the ultrasonic treatment mixture, then add 8 parts of polybenzimidazole to the ultrasonic treatment mixture, raise the temperature to 70°C, and keep it under nitrogen protection for 9 hours, cool to room temperature and filter after the reaction, filter the product with absolute ethanol Washing 2 to 3 times, and drying to obtain a composite reaction product;
[0028] (3) Add 60 parts of polyvinylidene chloride, 8 parts of sodium polystyrene sulfonate, 7 parts of me...
Embodiment 3
[0032] (1) Add 45 parts of polyethylene glycol diacrylate, 28 parts of alkyd resin, and 6 parts of nano-cerium oxide into the reaction kettle for mixing, then add the same mass of propyl acetate, stir at 80°C for 45 minutes, and the stirring speed For 600 rev / min, obtain the premixed liquid;
[0033] (2) Mix 32 parts of polyglycolic acid, 15 parts of bamboo fiber, 12 parts of vinyl bis stearamide, 5 parts of melamine polyphosphate and 200 parts of deionized water, and ultrasonicate for 25 minutes according to the ultrasonic treatment power of 500 W. Obtain the ultrasonic treatment mixture, then add 10 parts of polybenzimidazole to the ultrasonic treatment mixture, raise the temperature to 75°C, keep it under nitrogen protection for 10 hours, cool to room temperature and filter after the reaction, filter the product with absolute ethanol Washing 2 to 3 times, and drying to obtain a composite reaction product;
[0034](3) Add 65 parts of polyvinylidene chloride, 9 parts of sodi...
PUM
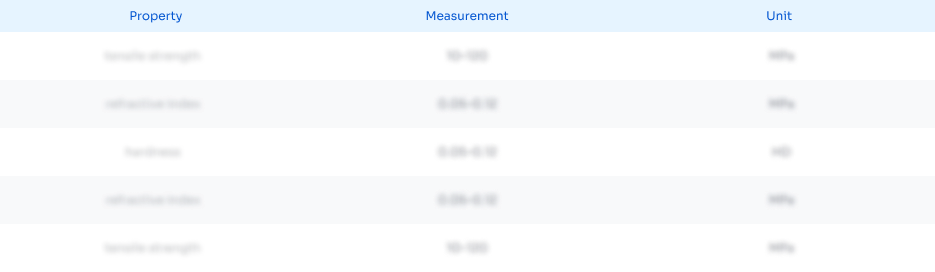
Abstract
Description
Claims
Application Information

- R&D Engineer
- R&D Manager
- IP Professional
- Industry Leading Data Capabilities
- Powerful AI technology
- Patent DNA Extraction
Browse by: Latest US Patents, China's latest patents, Technical Efficacy Thesaurus, Application Domain, Technology Topic, Popular Technical Reports.
© 2024 PatSnap. All rights reserved.Legal|Privacy policy|Modern Slavery Act Transparency Statement|Sitemap|About US| Contact US: help@patsnap.com