nio-y nanocomposite material and its preparation method and application
A technology of nano-composite materials and raw materials, applied in the field of Y molecular sieves loaded with NiO, can solve the problems of low gas production and small surface area, etc.
- Summary
- Abstract
- Description
- Claims
- Application Information
AI Technical Summary
Problems solved by technology
Method used
Image
Examples
Embodiment 1
[0041] Add 35 mL of deionized water and 3.16 g of glucose into a polytetrafluoroethylene container, stir at room temperature for 30 min, put it in a reaction kettle, seal it, place it in a constant temperature box, and heat it to 180 °C for a static crystallization reaction for 12 h. Take out the reaction kettle, quickly cool it to room temperature in a quenching tank, take out the reaction product, wash three times with deionized water and absolute ethanol respectively, filter with suction, dry in a vacuum drying box at 70°C for 12 hours, and grind to obtain carbon microsphere powder .
[0042] Take 30 mL of deionized water, 2.33 g of sodium hydroxide, 1.99 g of sodium metaaluminate, and 2.33 g of white carbon black, add them together into a polytetrafluoroethylene container, and stir at room temperature to form a sol solution. Add 0.5 g of carbon microspheres to the sol solution, adjust the pH to 13.5 with 98 wt% concentrated sulfuric acid, stir vigorously at 800 r / min for 2...
Embodiment 2
[0051] Carbon microspheres were prepared according to the method of Example 1.
[0052] Take 32 mL of deionized water, 1.185 g of sodium hydroxide, 3.41 g of sodium metaaluminate, and 1.78 g of white carbon black, add them together into a polytetrafluoroethylene container, and stir at room temperature to form a sol solution. Add 0.8 g of carbon microspheres to the sol solution, adjust the pH to 13.5 with 98 wt% concentrated sulfuric acid, stir vigorously at 1000 r / min for 2 h, and let it stand for 1 d in an airtight condition at room temperature. Then put it into a stainless steel reaction kettle, and heat it in a constant temperature oven to 90°C for constant temperature crystallization reaction for 12 hours. The reaction kettle was taken out, quenched, and the reaction product was taken out. After washing, suction filtration, drying, and calcination in a muffle furnace at 500°C for 5 hours, the nano-Y molecular sieve was prepared.
[0053] Weigh 0.12g Ni (NO 3 ) 2 ·6H 2 ...
Embodiment 3
[0055] Carbon microsphere powder was prepared according to the method of Example 1.
[0056] Take 34 mL of deionized water, 1.30 g of sodium hydroxide, 3.54 g of sodium metaaluminate, and 1.62 g of white carbon black, add them together into a polytetrafluoroethylene container, and stir at room temperature to form a sol solution. 1.25 g of carbon microspheres were added to the sol solution, the pH value was adjusted to 13.5 with 98wt% concentrated sulfuric acid, vigorously stirred at 1200 r / min for 3 h, and aged for 6 d at room temperature. Then put it into a stainless steel reaction kettle and heat it in a constant temperature oven to 90°C for constant temperature crystallization reaction for 16h. The reaction kettle was taken out, quenched, and the reaction product was taken out. After washing, suction filtration, drying, and roasting in a muffle furnace at 550 °C for 5 hours, the nano-Y molecular sieve was prepared.
[0057] Weigh 0.06g Ni (NO 3 ) 2 ·6H 2 O, 5 mL of deio...
PUM
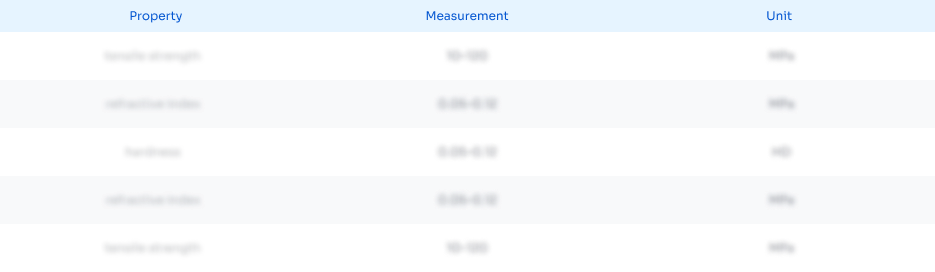
Abstract
Description
Claims
Application Information

- R&D Engineer
- R&D Manager
- IP Professional
- Industry Leading Data Capabilities
- Powerful AI technology
- Patent DNA Extraction
Browse by: Latest US Patents, China's latest patents, Technical Efficacy Thesaurus, Application Domain, Technology Topic, Popular Technical Reports.
© 2024 PatSnap. All rights reserved.Legal|Privacy policy|Modern Slavery Act Transparency Statement|Sitemap|About US| Contact US: help@patsnap.com