Preparation and application methods of Cu-Ni-based catalyst for reversed water gas reaction
A technology of reverse water gas and catalyst, which is applied in the field of preparation of Cu-Ni-based catalysts, can solve problems such as difficulty in regulation, and achieve the effects of low preparation cost, high activity, and good application prospects
- Summary
- Abstract
- Description
- Claims
- Application Information
AI Technical Summary
Problems solved by technology
Method used
Image
Examples
preparation example Construction
[0032] Among them, through the control of the preparation conditions and reaction conditions of the catalyst, as well as the optimization of a number of experimental parameters, the structure and catalytic performance of CuNi-NMs catalysts with high activity and 100% selectivity for CO production can be realized.
[0033] When the catalyst is prepared in the present invention, the copper salt is preferably copper nitrate, the nickel salt is preferably nickel acetate, and the selected metal salt may or may not contain crystal water. The concentration of copper is preferably 0.2-0.6M; the concentration of nickel is preferably 0.2-0.6M. The complexing agent is preferably disodium ethylenediaminetetraacetic acid (EDTA·2Na). The dosage of the complexing agent is preferably 1 to 2 times the total moles of cobalt and aluminum. In the co-complexation reaction, the heating temperature is preferably 75-85° C., and the reaction time is preferably 8-10 hours. The drying temperature of t...
Embodiment 1
[0036] (1) Weigh 0.05mol Cu(NO 3 ) 2 ·3H 2 O and 0.05mol Ni(CH 3 COO) 2 4H 2 O, stirring and dissolving in the mixed solution of 100mL water and ethanol (volume ratio H 2 O:EtOH=1:1), that is, Cu in the resulting solution 2+ The concentration is 0.5M, Ni 2+ The concentration is 0.5M. Weigh 0.05mol ethylenediaminetetraacetic acid, add it into the above mixed solution, and stir and react at 70°C for 8h. The resulting precipitate was aged, filtered and washed to obtain CuNi-LDH.
[0037] (2) The obtained CuNi-LDH was dried at 100°C for 10h, then calcined in a muffle furnace at 400°C for 4h, and cooled to room temperature to obtain CuNi-NTs.
[0038] (3) CuNi-NTs in flowing H 2 The reduction reaction is carried out in a mixed gas atmosphere with Ar, where H 2 The volume fraction of CuNi-NMs was controlled to be 10%, the gas flow rate was controlled to be 80sccm, the temperature was controlled to be 500°C, the reduction time was 4h, and after natural cooling to room temp...
Embodiment 2
[0041] (1) Weigh 0.04mol Cu(NO 3 ) 2 ·3H 2 O and 0.08mol Ni(NO 3 ) 2 ·6H 2 O, stirring and dissolving in the mixed solution of 200mL water and ethanol (volume ratio H 2 O:EtOH=2:1), that is, Cu in the resulting solution 2+ The concentration is 0.2M, Ni 2+ The concentration is 0.4M. Weigh 0.16 mol of disodium ethylenediaminetetraacetate, add it to the above mixed solution, and stir and react at 80°C for 10h. The resulting precipitate was aged, filtered and washed to obtain CuNi-LDH.
[0042] (2) The obtained CuNi-LDH was dried at 105°C for 12h, then calcined in a muffle furnace at 450°C for 5h, and cooled to room temperature to obtain CuNi-NTs.
[0043] (3) CuNi-NTs in flowing H 2 The reduction reaction is carried out in a mixed gas atmosphere with Ar, where H 2 The volume fraction of CuNi-NMs was controlled to be 12%, the gas flow rate was controlled to be 70sccm, the temperature was controlled to be 550°C, the reduction time was 3h, and after natural cooling to roo...
PUM
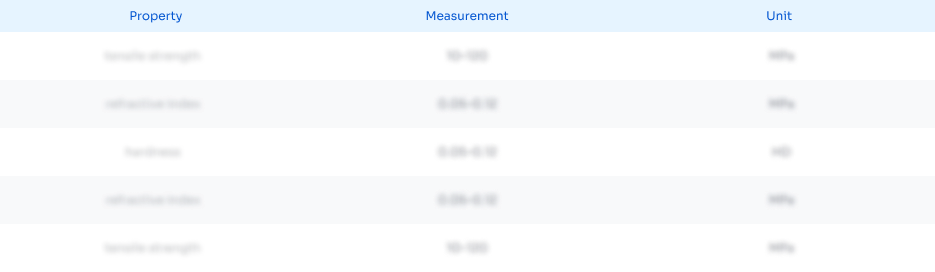
Abstract
Description
Claims
Application Information

- R&D
- Intellectual Property
- Life Sciences
- Materials
- Tech Scout
- Unparalleled Data Quality
- Higher Quality Content
- 60% Fewer Hallucinations
Browse by: Latest US Patents, China's latest patents, Technical Efficacy Thesaurus, Application Domain, Technology Topic, Popular Technical Reports.
© 2025 PatSnap. All rights reserved.Legal|Privacy policy|Modern Slavery Act Transparency Statement|Sitemap|About US| Contact US: help@patsnap.com