A preparation method for reducing leakage current of low-voltage electrode foil for aluminum electrolytic capacitors
An aluminum electrolytic capacitor and low-voltage electrode technology, applied in electrolytic capacitors, capacitors, electrolytic coatings, etc., can solve the problem of large leakage current, and achieve the effect of small leakage current, avoiding damage and reducing leakage current.
- Summary
- Abstract
- Description
- Claims
- Application Information
AI Technical Summary
Problems solved by technology
Method used
Image
Examples
Embodiment 1
[0035] A preparation method for reducing the leakage current of a low-voltage electrode foil for an aluminum electrolytic capacitor, comprising the steps of:
[0036] S1. Immerse the low-voltage corrosion foil in the 3-aminopropyltrimethoxysilane coupling agent solution at 50°C, apply a voltage of 5V, and the formation time is 15min;
[0037] S2. Then place it in an aqueous ammonium adipate solution with a mass percentage of 8% to carry out secondary formation and tertiary formation successively. The formation voltages are 50V and 90V respectively, the formation temperature is 85°C, and the formation time is 10min. Treat in pure water at 100°C (boiling water) for 5 minutes;
[0038]S3. The electrode foil is placed in 5% boric acid by mass percentage and 10% borax by mass percentage. At 85°C, reverse power is applied once, with a voltage of 90V (same as the third-level voltage), and the power-on time is 3min;
[0039] S4. Heat treatment at a high temperature of 500°C for 2 min...
Embodiment 2
[0042] A preparation method for reducing the leakage current of a low-voltage electrode foil for an aluminum electrolytic capacitor, comprising the steps of:
[0043] S1. Immerse the low-pressure corroded foil in the vinyltrimethoxysilane coupling agent at 50°C (the mass percentage of the silane coupling agent is 2%, and the pH value is 4), apply a voltage of 8V, and the formation time is 5min;
[0044] S2. Place in 8% by mass ammonium adipate aqueous solution to carry out secondary formation and tertiary formation in sequence, the formation voltages are 50V and 90V respectively, the formation temperature is 85°C, and the formation time is 10min, and then at 90-100 ℃ pure water treatment for 5 minutes;
[0045] S3. Place the electrode foil in a solution of 5% by mass of boric acid and 10% by mass of borax, and at 50°C, apply reverse power once, with a voltage of 90V (same as the third-level voltage), and the power-on time is 3min;
[0046] S4. Heat treatment at a high tempera...
Embodiment 3
[0049] A preparation method for reducing the leakage current of a low-voltage electrode foil for an aluminum electrolytic capacitor, comprising the steps of:
[0050] S1. The low-pressure corroded foil is immersed in an aminopropylmethyldiethoxysilane coupling agent solution at 50°C (the mass percentage of the silane coupling agent is 0.5%, and the pH value is 3), and a voltage of 5V is applied, and the formation time is 10min;
[0051] S2. Place in 8% by mass ammonium adipate aqueous solution to carry out secondary formation and tertiary formation in sequence, the formation voltages are 50V and 90V respectively, the formation temperature is 85°C, and the formation time is 10min, and then at 90-100 ℃ pure water treatment for 5 minutes;
[0052] S3. The electrode foil is placed in boric acid with a mass percentage of 5% and borax with a mass percentage of 10%. At 90°C, a reverse power is applied once, with a voltage of 90V (same as the third-level voltage), and the power-on ti...
PUM
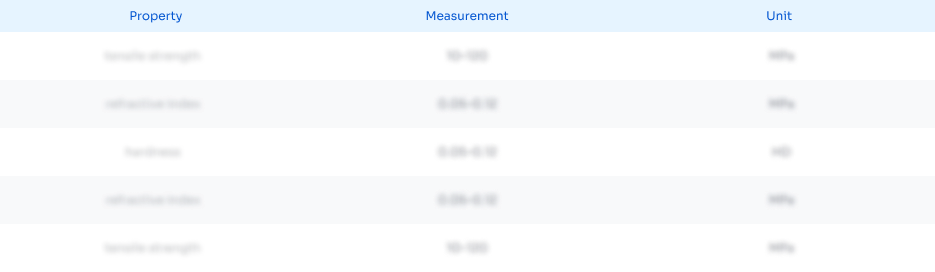
Abstract
Description
Claims
Application Information

- R&D
- Intellectual Property
- Life Sciences
- Materials
- Tech Scout
- Unparalleled Data Quality
- Higher Quality Content
- 60% Fewer Hallucinations
Browse by: Latest US Patents, China's latest patents, Technical Efficacy Thesaurus, Application Domain, Technology Topic, Popular Technical Reports.
© 2025 PatSnap. All rights reserved.Legal|Privacy policy|Modern Slavery Act Transparency Statement|Sitemap|About US| Contact US: help@patsnap.com