Sound pressure sensitivity calibration cavity and testing method thereof
A technology of sensitivity and standard cavity, which is applied in the field of sound pressure sensitivity calibration cavity and its testing, can solve the problems that the coupled cavity reciprocity method cannot realize the phase sensitivity calibration, the limitation of the test object, the uncertainty of the sound pressure sensitivity measurement, etc., and achieve the acoustic emission Good performance and reciprocity, realize phase sensitivity calibration, and reduce measurement error
- Summary
- Abstract
- Description
- Claims
- Application Information
AI Technical Summary
Problems solved by technology
Method used
Image
Examples
Embodiment Construction
[0021] The present invention will be described in detail below in conjunction with accompanying drawing:
[0022] The technical scheme adopted in the present invention: a sound pressure sensitivity calibration cavity and its testing method, the cavity body is composed of a standard cavity and a measuring cavity, and the testing method is the four-transducer reciprocal method, that is, firstly, the standard cavity is used to transmit The transducer and the reciprocal transducer are used to measure the transfer impedance and the reciprocal constant J of the coupling cavity, and then the transmitting transducer, the reciprocal transducer, and the hydrophone under test are installed in the measurement cavity, and another auxiliary transmitting The transducer transmits signals, and the first three are used as receivers, so as to realize the calibration of sound pressure sensitivity and phase sensitivity.
[0023] The standard cavity must be small enough for the lumped parameter mod...
PUM
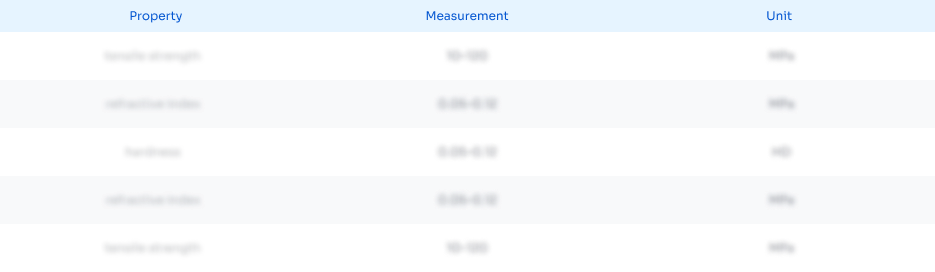
Abstract
Description
Claims
Application Information

- Generate Ideas
- Intellectual Property
- Life Sciences
- Materials
- Tech Scout
- Unparalleled Data Quality
- Higher Quality Content
- 60% Fewer Hallucinations
Browse by: Latest US Patents, China's latest patents, Technical Efficacy Thesaurus, Application Domain, Technology Topic, Popular Technical Reports.
© 2025 PatSnap. All rights reserved.Legal|Privacy policy|Modern Slavery Act Transparency Statement|Sitemap|About US| Contact US: help@patsnap.com