Aluminum nitride powder as well as preparation method and application thereof
An aluminum nitride and powder technology, applied in the field of aluminum nitride powder and its preparation, can solve the problems of insufficient carbothermic reduction reaction, affecting the contact of reaction gas, and poor gas path, etc., and achieves easy batch-to-batch performance. The effect of controlling, improving process capacity, and mixing fully and uniformly
- Summary
- Abstract
- Description
- Claims
- Application Information
AI Technical Summary
Problems solved by technology
Method used
Image
Examples
Embodiment 1
[0034] a. Add α-Al 2 o 3 The particles and petroleum carbon black are put into a dry ball mill for ball milling for 2 hours according to the mass ratio of 2:1 to obtain a mixed powder;
[0035] b. Mix and granulate the mixed powder, PVA and deionized water according to the mass ratio of 10:1.5:7, put the granulated particles into a drying furnace for debinding, and prepare a precursor with an average particle size of 2-10mm particles;
[0036] c. Send the precursor particles into a vertical graphite continuous synthesis furnace for continuous reaction in a nitrogen atmosphere to produce carbon-containing aluminum nitride particles, wherein the reaction temperature in the furnace is 1600 ° C, and the pressure in the furnace is 1000 Pa; The bulk particles naturally fall through the high temperature zone in the furnace from top to bottom, the residence time in the high temperature zone is 6h, and the flow rate is 6m 3 / The nitrogen gas of h flows through the high temperature z...
Embodiment 2
[0039] a. Add α-Al 2 o 3 The particles and natural carbon black are put into a dry ball mill for ball milling for 5 hours according to a mass ratio of 1.5:1 to obtain a mixed powder;
[0040] b. Mix and granulate the mixed powder, phenolic resin and deionized water according to the mass ratio of 10:0.5:8, put the granulated granules into a drying oven for debinding, and prepare a precursor with an average particle size of 2-10mm body particles;
[0041] c. Send the precursor particles into a vertical graphite continuous synthesis furnace for continuous reaction in a nitrogen atmosphere to produce carbon-containing aluminum nitride particles, wherein the reaction temperature in the furnace is 1800°C, and the pressure in the furnace is 2000Pa; The bulk particles naturally fall through the high temperature zone in the furnace from top to bottom, the residence time in the high temperature zone is 15h, and the flow rate is 18m 3 / h nitrogen gas flows through the high temperature z...
Embodiment 3
[0044] a. Add α-Al 2 o 3 The particles and acetylene carbon black were put into a dry ball mill for ball milling for 8 hours according to a mass ratio of 2.5:1 to obtain a mixed powder;
[0045] b. Mix the mixed powder, epoxy resin and absolute ethanol according to the mass ratio of 10:2:4 and then granulate. Put the granulated particles into the drying oven for debinding to prepare the average particle size 2-10mm precursor particles;
[0046] c. Send the precursor particles into a vertical graphite continuous synthesis furnace for continuous reaction in a nitrogen atmosphere to produce carbon-containing aluminum nitride particles, wherein the reaction temperature in the furnace is 1700°C, and the pressure in the furnace is 2000Pa; The bulk particles naturally fall through the high temperature zone in the furnace from top to bottom, the residence time in the high temperature zone is 10h, and the flow rate is 10m 3 / The nitrogen gas of h flows through the high temperature z...
PUM
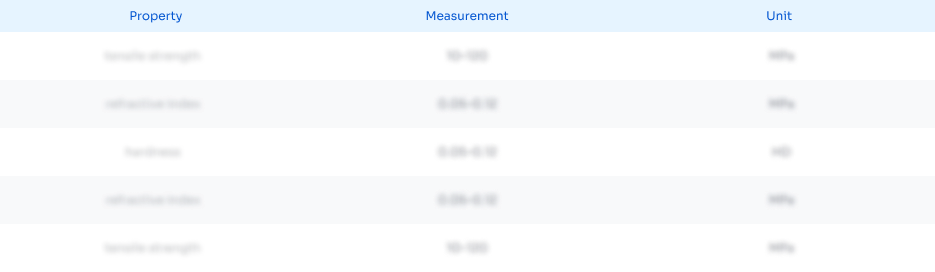
Abstract
Description
Claims
Application Information

- R&D
- Intellectual Property
- Life Sciences
- Materials
- Tech Scout
- Unparalleled Data Quality
- Higher Quality Content
- 60% Fewer Hallucinations
Browse by: Latest US Patents, China's latest patents, Technical Efficacy Thesaurus, Application Domain, Technology Topic, Popular Technical Reports.
© 2025 PatSnap. All rights reserved.Legal|Privacy policy|Modern Slavery Act Transparency Statement|Sitemap|About US| Contact US: help@patsnap.com