Rolling roller set system for rolling waste railway steel rail
A roll set and rail technology, which is applied in the field of rolling roll set system for rolling waste railway rails, can solve the problems of material waste, high energy consumption, and irregular edges of raw materials, etc.
- Summary
- Abstract
- Description
- Claims
- Application Information
AI Technical Summary
Problems solved by technology
Method used
Image
Examples
Embodiment Construction
[0018] Such as figure 1 As shown, the rolling roll group system for rolling scrap railway rails of the present invention, the first rolling roll group A1A2 is a rolling roll group that expands grooves along the railway rail hole shape after being heated, and the second rolling roll group The rolling roll group B1B2 is the rolling roll group for indentation rolling along the boundary line of the rail top, rail waist and rail bottom after the groove expansion in the previous process, and it will be added after the second rolling roll group A set of rolling rolls C1C2 for forming deeper indentations. One of the rolling rolls in the second rolling roll group B1B2 uses one of the rolling rolls in the first rolling roll set A1A2, the overall position is staggered from the first rolling roll group, and the third rolling roll group C1C2 It is designed to stagger with the first two rolling roll groups on the overall position at the position away from the first two rolling roll groups ...
PUM
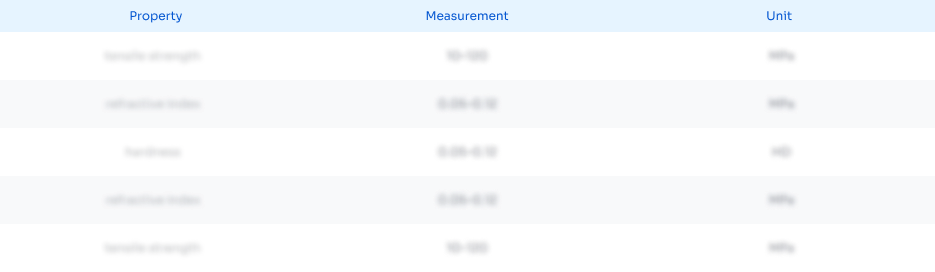
Abstract
Description
Claims
Application Information

- R&D Engineer
- R&D Manager
- IP Professional
- Industry Leading Data Capabilities
- Powerful AI technology
- Patent DNA Extraction
Browse by: Latest US Patents, China's latest patents, Technical Efficacy Thesaurus, Application Domain, Technology Topic, Popular Technical Reports.
© 2024 PatSnap. All rights reserved.Legal|Privacy policy|Modern Slavery Act Transparency Statement|Sitemap|About US| Contact US: help@patsnap.com