A method of catalytic cracking
A catalytic cracking and catalyst technology, which is applied in the treatment of hydrocarbon oil, petroleum industry, hydrotreating process, etc., can solve the problems of increased coke yield, achieve reduced coke yield, increase gasoline yield, and better product selectivity Effect
- Summary
- Abstract
- Description
- Claims
- Application Information
AI Technical Summary
Problems solved by technology
Method used
Image
Examples
Embodiment 1
[0071] This embodiment illustrates adopting the method provided by the present invention, carried out in a medium-sized catalytic cracking unit and a medium-sized hydrogenation unit, and the specific process refers to figure 1 .
[0072] First, the light cycle oil E is sent to the medium-sized hydrogenation unit 10 to contact with the hydrotreating catalyst to carry out the hydrogenation treatment of the hydrogenation saturation of aromatic hydrocarbons to obtain the hydrogenated light cycle oil F, and the hydrogenated light cycle oil F is sent to the raw material tank (height 60 centimeters, volume 75 liters) 16, mixed with feedstock A as catalytic cracking feedstock oil, feedstock A and hydrogenated light cycle oil F are mixed according to the weight ratio of 3.84:1, mixing conditions are: stirring speed is 60 rpm / min, with continuous stirring. The mixed raw oil C is sent to a medium-sized catalytic cracking unit for reaction, and the catalyst used is CGP-1. The specific o...
Embodiment 2
[0074] This example illustrates the use of the method provided by the invention for catalytic cracking, which is carried out in a medium-sized catalytic cracking unit and a medium-sized hydrogenation unit, and the specific process refers to figure 1 .
[0075] The specific operation method is basically the same as that of Example 1, except that the raw material oil B is used as the catalytic cracking raw material oil, and the self-produced light cycle oil J is used for hydrogenation treatment to obtain hydrogenated light cycle oil L as light oil, and the obtained mixed The raw material oil D1 was sent to a medium-sized catalytic cracking unit for reaction, and the catalyst was ASC-4. See Table 5 for specific operating conditions and product distribution.
Embodiment 3
[0077] This example illustrates that catalytic cracking is carried out using the method provided by the present invention, which is carried out in a medium-sized catalytic cracking unit and a medium-sized hydrogenation unit, and the specific process refers to figure 1 .
[0078] First, the light cycle oil J and the oil slurry K are mixed according to the weight ratio of 1:1.29, and sent to the filter device to filter to obtain the separated fraction oil M, and the separated fraction oil M is sent to the medium-sized hydrogenation unit 10 to contact with the hydrotreating catalyst. Aromatic hydrogenation and saturation hydrogenation treatment to obtain hydrogenated and separated distillate N, which is sent to the raw material tank 16 as light oil and mixed with fresh raw material B as catalytic cracking raw material oil. The fresh raw material The mixing weight ratio of B and hydrogenated distillate oil N is 2.28:1, and the mixing conditions are: the stirring speed is 60 rpm, a...
PUM
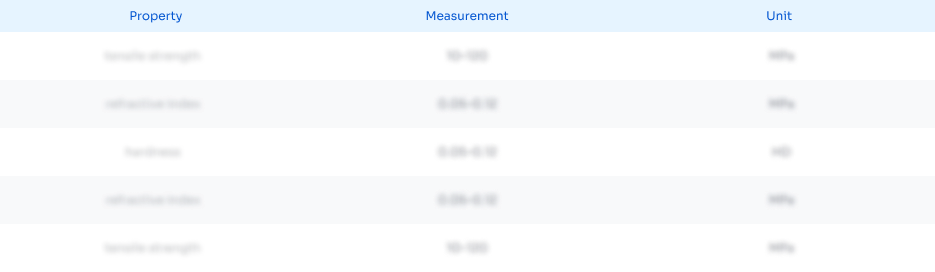
Abstract
Description
Claims
Application Information

- R&D Engineer
- R&D Manager
- IP Professional
- Industry Leading Data Capabilities
- Powerful AI technology
- Patent DNA Extraction
Browse by: Latest US Patents, China's latest patents, Technical Efficacy Thesaurus, Application Domain, Technology Topic, Popular Technical Reports.
© 2024 PatSnap. All rights reserved.Legal|Privacy policy|Modern Slavery Act Transparency Statement|Sitemap|About US| Contact US: help@patsnap.com