Insulating tape and preparation method thereof
A technology of insulating tape and resin mixture, applied in the field of materials, can solve the problems of complicated operation and large dependence on construction process, and achieve the effects of high breakdown voltage, avoiding on-site mixing operation and simple construction.
- Summary
- Abstract
- Description
- Claims
- Application Information
AI Technical Summary
Problems solved by technology
Method used
Image
Examples
preparation example Construction
[0020] The preparation method of insulating tape provided by the invention comprises the following steps:
[0021] Preparation of insulating tape:
[0022] Such as figure 1 As shown in step S101, the polyester polyol oxygen, flame retardant, talcum powder and carbon black are mixed to obtain a resin mixture, specifically, according to the number of parts by mass, 80-120 parts of polyester polyol oxygen , 5-20 parts of flame retardant, 10-50 parts of talcum powder and 10-200 parts of carbon black are added to the kneader respectively, and kneaded for 10-30 minutes to obtain the resin mixture; preferably, according to parts by mass In counting, 100 parts of polyester polyol oxygen, 10 parts of flame retardant, 30 parts of talcum powder and 100 parts of carbon black were added to the kneader respectively, and kneaded for 20 minutes to obtain the resin mixture; wherein, Polyester Polyol Oxygen C 4 -C 30 Polyester polyol oxygen. The flame retardant is selected from antimony tr...
Embodiment 1
[0027] 1) Add commercially available polysiloxane acrylate, magnesium hydroxide flame retardant, talcum powder and carbon black to the kneader, wherein the mass ratio: polysiloxane acrylate is 100 parts, magnesium hydroxide flame retardant 5 parts of agent, 10 parts of talcum powder, and 10 parts of carbon black were kneaded for 15 minutes to obtain a resin mixture.
[0028] 2) Add an isocyanate curing agent into the resin mixture, 100 parts of the resin mixture, 5 parts of the isocyanate curing agent to obtain the final product.
[0029] 3) The final product is calendered into coils of corresponding thickness with a calender, coated with PET film on both sides, sliced, and vacuum-packed with aluminum-coated packaging to obtain the final product.
[0030] 4) Test the hardness, breakdown voltage, UV accelerated aging performance, flame retardancy and waterproof performance after curing.
Embodiment 2
[0032] 1) Add commercially available adipic acid polyester diol, antimony trioxide flame retardant, talcum powder and carbon black, etc. into the kneader, wherein the mass ratio: adipic acid polyester diol is 120 parts, trioxide 20 parts of diantimony flame retardant, 50 parts of talcum powder, and 150 parts of carbon black were kneaded for 30 minutes to obtain a resin mixture.
[0033] 2) Add phenolsulfonic acid curing agent to the resin mixture, 100 parts of the resin mixture, 50 parts of the isocyanate curing agent to obtain the final product.
[0034] 3) The final product is calendered into coils of corresponding thickness with a calender, coated with PET film on both sides, sliced, and vacuum-packed with aluminum-coated packaging to obtain the final product.
[0035] 4) Test the hardness, breakdown voltage, UV accelerated aging performance, flame retardancy and waterproof performance after curing.
PUM
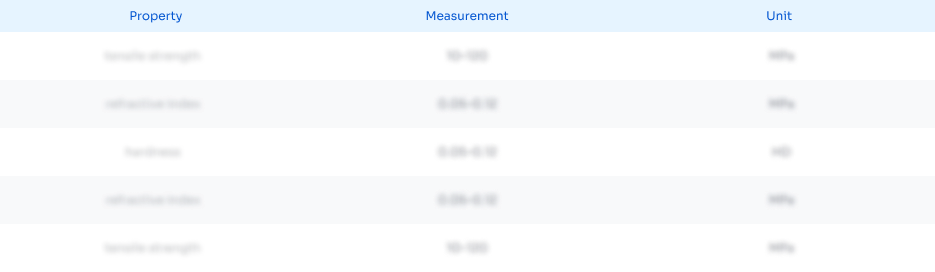
Abstract
Description
Claims
Application Information

- R&D Engineer
- R&D Manager
- IP Professional
- Industry Leading Data Capabilities
- Powerful AI technology
- Patent DNA Extraction
Browse by: Latest US Patents, China's latest patents, Technical Efficacy Thesaurus, Application Domain, Technology Topic, Popular Technical Reports.
© 2024 PatSnap. All rights reserved.Legal|Privacy policy|Modern Slavery Act Transparency Statement|Sitemap|About US| Contact US: help@patsnap.com