Anti-icing film and preparation method thereof
An anti-icing and thin-film technology, applied in chemical instruments and methods, other chemical processes, coatings, etc., can solve the problems of limited anti-icing and deicing capabilities, reduced anti-icing performance, and high ice adhesion strength. To achieve the effects of easy operation and promotion, increased service life, and simple preparation method
- Summary
- Abstract
- Description
- Claims
- Application Information
AI Technical Summary
Problems solved by technology
Method used
Image
Examples
preparation example Construction
[0021] The preparation method of the anti-icing film provided by the present invention comprises the following steps:
[0022] like figure 1 Step S101 shown in step S101: after the low surface energy resin and the conductive filler are mixed uniformly, the crosslinking agent and the catalyst are added, and the mixture is uniformly mixed to prepare a mixture. In this step, by weight, 90-110 parts of low surface resin and 1-10 parts of conductive filler are stirred at a stirring speed of 400-600 r / min for 20-40 minutes, and after mixing uniformly, 10-30 parts are added The crosslinking agent and 1-5 parts of the catalyst are stirred for 7-15 minutes at a stirring speed of 700-900 r / min, and the mixture is uniformly mixed to obtain a mixture. In this step, sufficient stirring is required to ensure that the conductive filler is evenly dispersed in the low surface energy resin to form a conductive grid, thereby ensuring that the film has good conductivity. The low surface energy ...
Embodiment 1
[0029] In parts by weight, 100 parts of silicone rubber and 1 part of carbon nanotubes were stirred at a stirring speed of 400 r / min for 35 minutes, after mixing evenly, 10 parts of ethyl silicate and 1 part of dibutyltin dilaurate were added, The mixture was stirred for 10 minutes at a stirring speed of 800 r / min, and the mixture was uniformly mixed to obtain a mixture. The surface of the substrate is washed with ethanol, and after the surface of the substrate is dried and cleaned, the mixture is coated on the surface of the substrate using a film coater to form a coating on the surface of the substrate. The coating was cured in an oven at 90° C. for 30 min, and an anti-icing film was prepared after the coating was completely cured.
[0030] The contact angle of the anti-icing film measured by the pendant drop method using a contact angle tester is 110°, and the anti-icing film generates heat after electrification.
Embodiment 2
[0032] In parts by weight, 100 parts of fluorocarbon resin and 10 parts of graphite were stirred at a stirring speed of 600r / min for 20 minutes. After mixing evenly, 15 parts of butyl titanate and 3 parts of stannous octoate were added, and the mixture was stirred at 700r / min. The mixture was stirred for 15 minutes at a stirring speed of 100 Å, and the mixture was uniformly mixed to obtain a mixture. The surface of the substrate is washed with acetone, and after the surface of the substrate is dried and cleaned, the mixture is coated on the surface of the substrate using a film coater to form a coating on the surface of the substrate. The coating was cured in an oven at 100° C. for 35 min, and after the coating was completely cured, an anti-icing film was prepared.
[0033] The contact angle of the anti-icing film measured by the pendant drop method using a contact angle tester is 115°, and the anti-icing film generates heat after electrification.
PUM
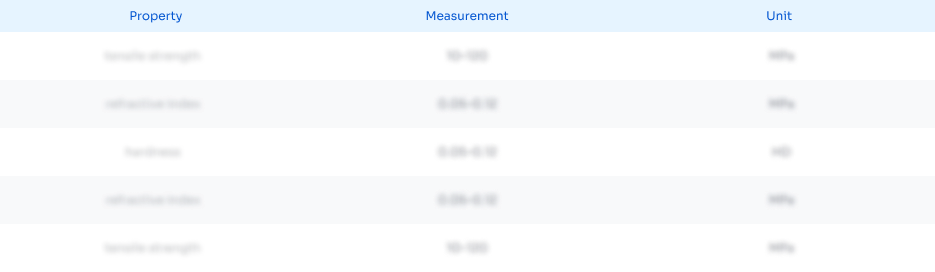
Abstract
Description
Claims
Application Information

- R&D
- Intellectual Property
- Life Sciences
- Materials
- Tech Scout
- Unparalleled Data Quality
- Higher Quality Content
- 60% Fewer Hallucinations
Browse by: Latest US Patents, China's latest patents, Technical Efficacy Thesaurus, Application Domain, Technology Topic, Popular Technical Reports.
© 2025 PatSnap. All rights reserved.Legal|Privacy policy|Modern Slavery Act Transparency Statement|Sitemap|About US| Contact US: help@patsnap.com