Coating material used for preventing locking of engine crankshaft, and preparation method and usage method thereof
A coating material and engine technology, used in anti-corrosion coatings, fire-resistant coatings, crankshafts, etc., can solve problems such as inability to provide effective lubrication, locking, and insufficient lubrication, to prevent metal sintering and sticking, reduce failures, and prevent Effect of fretting wear characteristics
- Summary
- Abstract
- Description
- Claims
- Application Information
AI Technical Summary
Problems solved by technology
Method used
Examples
Embodiment 1
[0028] The coating material used to prevent engine crankshaft from locking in the present embodiment, the coating material raw material is made up of the following components by weight: 60 parts of PAG polyether base oil, 25 parts of modified plant-based synthetic ester oxidized sunflower oil, 5 parts of epoxy resin, 2 parts of organic molybdenum, 5 parts of tungsten disulfide powder, 5 parts of tungsten diselenide powder, 10 parts of fluorinated graphite powder, 7 parts of polyphenylene, 2 parts of flame retardant, 3 parts of anti-wear agent, Antioxidant 0.2 part.
[0029] In this example, the organic molybdenum is oxymolybdenum dialkyldithiophosphate. In this example, the oxymolybdenum dialkyldithiophosphate is replaced by nitrogen-containing dialkyldisulfide One of oxymolybdenum phosphate, molybdenum dialkyldithiocarbamate, molybdenum amine complex, molybdenum naphthenate, and molybdenum alkyl salicylate; or replace it with dialkyldithiocarbamate in equal parts The mixture...
Embodiment 2
[0036] The coating material used to prevent the engine crankshaft from locking in the present embodiment, the coating material raw material is made up of the following components by weight: 50 parts of PAG polyether base oil, 15 parts of modified plant-based synthetic ester oxidized sunflower oil, 3 parts of epoxy resin, 1 part of organic molybdenum, 5 parts of tungsten disulfide powder, 3 parts of tungsten diselenide powder, 5 parts of fluorinated graphite powder, 5 parts of polyphenylene, 1 part of flame retardant, 1 part of anti-wear agent, Antioxidant 0.1 part.
[0037] In this embodiment, the organic molybdenum is nitrogen-containing dialkyl molybdenum dithiophosphate. In this embodiment, the nitrogen-containing dialkyl dithiophosphate oxymolybdenum is replaced by dialkyl One of oxymolybdenum dithiophosphate, molybdenum dialkyldithiocarbamate, molybdenum amine complex, molybdenum naphthenate, and molybdenum alkyl salicylate; or replace it with nitrogen-containing dioxane ...
Embodiment 3
[0044] The coating material used to prevent engine crankshaft from locking, the coating material raw material is composed of the following components by weight: 70 parts of PAG polyether base oil, 30 parts of modified plant-based synthetic ester oxidized sunflower oil, 8 parts of epoxy resin Parts, 5 parts of organic molybdenum, 10 parts of tungsten disulfide powder, 7 parts of tungsten diselenide powder, 15 parts of graphite fluoride powder, 10 parts of polystyrene, 3 parts of flame retardant, 5 parts of antiwear agent, 0.5 parts of antioxidant share.
[0045] In this embodiment, the organic molybdenum is molybdenum dialkyldithiocarbamate. In this embodiment, the molybdenum dialkyldithiocarbamate is replaced by nitrogen-containing dialkyldisulfide One of oxymolybdenum phosphate, oxymolybdenum dialkyl dithiophosphate, molybdenum amine complex, molybdenum naphthenate, and molybdenum alkyl salicylate; or replace it with dialkyl dithio The mixture of molybdenum carbamate and nit...
PUM
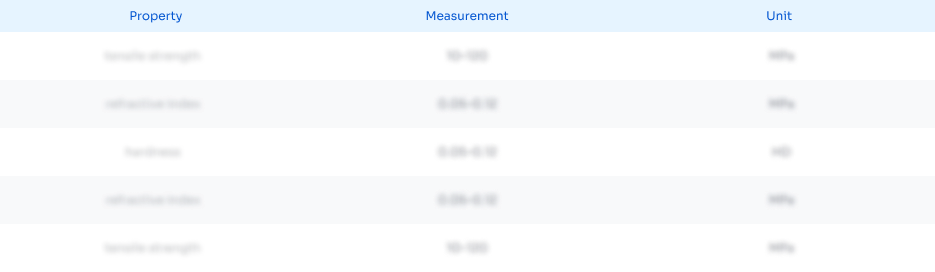
Abstract
Description
Claims
Application Information

- Generate Ideas
- Intellectual Property
- Life Sciences
- Materials
- Tech Scout
- Unparalleled Data Quality
- Higher Quality Content
- 60% Fewer Hallucinations
Browse by: Latest US Patents, China's latest patents, Technical Efficacy Thesaurus, Application Domain, Technology Topic, Popular Technical Reports.
© 2025 PatSnap. All rights reserved.Legal|Privacy policy|Modern Slavery Act Transparency Statement|Sitemap|About US| Contact US: help@patsnap.com