Numerical control pipe bending machine of improved structure
A technology of structure improvement and pipe bending machine, which is applied in the field of pipe processing equipment, can solve problems such as interference, interference during bending pipe forming process, unfavorable bending and forming pipe bending structure, etc., and achieve the effects of reducing interference, optimizing layout and improving precision
- Summary
- Abstract
- Description
- Claims
- Application Information
AI Technical Summary
Problems solved by technology
Method used
Image
Examples
Embodiment 1
[0038] see Figure 1 to Figure 14 , The CNC pipe bending machine includes a frame, a control unit, a machine head 1 and a feeding trolley installed on the frame and controlled by the control unit. The machine head includes a mold changing unit 2, a machine head base 3, a mold guide unit 4 installed on the machine head base 3, a pipe bending motor 10, a pipe bending main shaft and a pipe bending torque transmission mechanism, which are coaxially installed on the pipe bending main shaft The circular mold 12 and the swing arm 5 on the top, and the clamping mold 13 and the clamping mold drive mechanism 6 installed on the swing arm 5. The pipe bending torque transmission mechanism is used to transmit the torque output by the pipe bending motor 10 to the pipe bending main shaft, so as to drive the clamping die 13 and the round die 12 to rotate synchronously, so as to form the pipe blank into a corresponding curved pipe structure.
[0039] In this embodiment, the control unit includ...
Embodiment 2
[0067] As an illustration of Embodiment 2 of the present invention, only the differences from Embodiment 1 above will be described below.
[0068] see Figure 15 to Figure 17, in this embodiment, a ball screw mechanism is used instead of the above-mentioned planetary roller screw mechanism to construct the clamping drive mechanism 6 . Correspondingly, the reduction transmission mechanism adopts a gear train reduction box 64 , and the support seat is a reduction box body 640 fixed on the swing end of the swing arm 5 .
[0069] Clamping base 63 comprises the bottom plate 631 that is connected with the slide block on the rolling guide rail 630, is fixed on the box-type seat portion 632 on one end portion of the base plate 631 adjacent to the elbow main shaft, and is fixed on the box-type seat portion 632 away from the bend. One side of the pipe main shaft and the triangular reinforcing rib 633 between the other end of the bottom plate 631; the clamping mold 13 is detachably fixe...
PUM
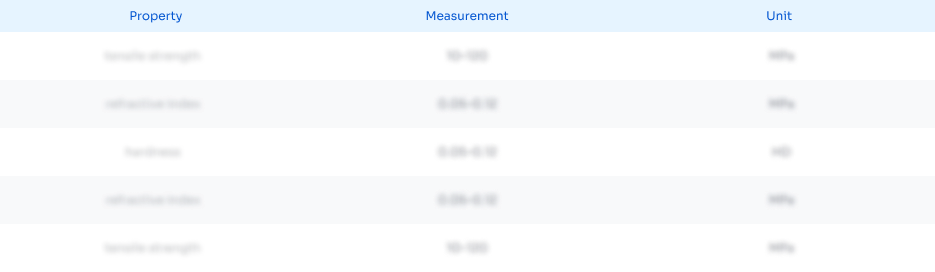
Abstract
Description
Claims
Application Information

- R&D Engineer
- R&D Manager
- IP Professional
- Industry Leading Data Capabilities
- Powerful AI technology
- Patent DNA Extraction
Browse by: Latest US Patents, China's latest patents, Technical Efficacy Thesaurus, Application Domain, Technology Topic, Popular Technical Reports.
© 2024 PatSnap. All rights reserved.Legal|Privacy policy|Modern Slavery Act Transparency Statement|Sitemap|About US| Contact US: help@patsnap.com