Alloy material, lightweight brake drum with alloy material applied, and lightweight brake drum preparation method
An alloy material, lightweight technology, used in brake drums, manufacturing tools, heat treatment equipment, etc., can solve problems such as single improvement point, inability to improve performance in all directions, cracking, etc., to improve safety and increase braking stability. , the effect of long life
- Summary
- Abstract
- Description
- Claims
- Application Information
AI Technical Summary
Problems solved by technology
Method used
Image
Examples
Embodiment 1
[0038] The lightweight brake drum structure is as figure 1 , figure 2 As shown, it includes a friction body 1 and a base 2. The friction body 1 is evenly provided with 16 groups of venting and chip removal holes 3 arranged uniformly along the central axis of the lightweight brake drum, and the number of ventilation chip removal holes 3 in each group is There are 5, and the diameter of each venting chip hole is 20mm.
[0039] The diameter of the lightweight brake drum in this embodiment is 400 mm, and the wall thickness of the friction body is 15.5 mm.
[0040] The preparation method of the lightweight brake drum in this embodiment includes the following steps:
[0041] (1) Using ANSYS structural optimization and strength checking, design the core box and cavity model of the lightweight brake drum;
[0042] (2) Put the commonly used raw materials for alloy smelting into the electric furnace for smelting, and use a spectrometer to perform rapid analysis and detection before the furnac...
Embodiment 2
[0050] This embodiment provides a lightweight brake drum. The structure of the lightweight brake drum is as described in Embodiment 1, wherein there are 8 groups of ventilation and chip removal holes, and the number of ventilation and chip removal holes 3 in each group is 6. , The diameter of the ventilation chip hole 3 is 16mm.
[0051] The diameter of the lightweight brake drum in this embodiment is 240 mm, and the wall thickness of the friction body is 10.4 mm.
[0052] (1) Using ANSYS structural optimization and strength checking, design the core box and cavity model of the lightweight brake drum;
[0053] (2) Put the commonly used raw materials for alloy smelting into the electric furnace for smelting, and use a spectrometer to perform rapid analysis and detection before the furnace to adjust the feeding, until the element composition of the melt is: C 0.24wt%; Si 0.48wt%; Mn 1.09wt%; S0.006wt%; P 0.007wt%; Ni 1.08wt%; Cr 0.88wt%; Mo 0.52wt%; Al 0.018wt%; the rest is iron;
[00...
Embodiment 3
[0061] This embodiment provides a lightweight brake drum. The structure of the lightweight brake drum is as described in Embodiment 1, wherein there are 12 groups of ventilation and chip removal holes 3, and the number of ventilation and chip removal holes 3 in each group is 5, each venting chip hole diameter is 10mm.
[0062] The diameter of the lightweight brake drum in this embodiment is 200 mm, and the wall thickness of the friction body is 9.8 mm.
[0063] The preparation method of the lightweight brake drum in this embodiment includes the following steps:
[0064] (1) Using ANSYS structural optimization and strength checking, design the core box and cavity model of the lightweight brake drum;
[0065] (2) Put the common raw materials for alloy smelting into the electric furnace for smelting, and use a spectrometer to perform rapid analysis and detection before the furnace to adjust the feeding, until the element composition of the melt is: C 0.25wt%; Si 0.5wt%; Mn 1.08wt%; S 0....
PUM
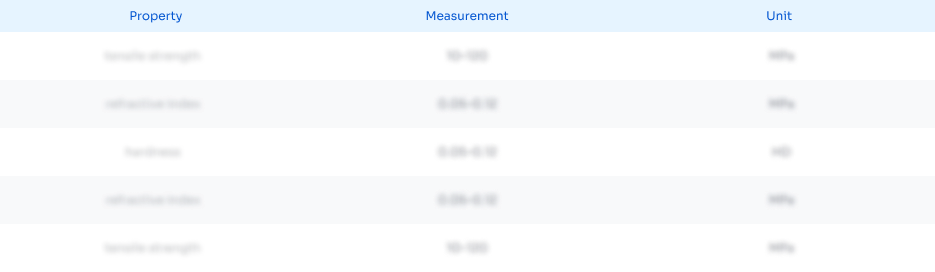
Abstract
Description
Claims
Application Information

- Generate Ideas
- Intellectual Property
- Life Sciences
- Materials
- Tech Scout
- Unparalleled Data Quality
- Higher Quality Content
- 60% Fewer Hallucinations
Browse by: Latest US Patents, China's latest patents, Technical Efficacy Thesaurus, Application Domain, Technology Topic, Popular Technical Reports.
© 2025 PatSnap. All rights reserved.Legal|Privacy policy|Modern Slavery Act Transparency Statement|Sitemap|About US| Contact US: help@patsnap.com