Low-rhenium high-strength thermal-corrosion-resistant nickel-based single-crystal high-temperature alloy and manufacturing method thereof
A nickel-based single crystal, superalloy technology, applied in nickel-based single crystal superalloy and its manufacture, hot-end components under high pressure, high load and high corrosion conditions, high temperature blades of heavy gas turbines, prepared in high temperature fields , can solve the problems of increased alloy cost, increased density, and easy precipitation of TCP, and achieve good high-temperature durability, strong hot-corrosion resistance, and improved mechanical properties
- Summary
- Abstract
- Description
- Claims
- Application Information
AI Technical Summary
Problems solved by technology
Method used
Examples
Embodiment 1
[0033] The chemical composition weight percent of the designed alloy is: Cr: 9.8%, Co: 9.6%, Mo: 0.7%, W: 5.4%, Al: 4.5%, Ti: 2.93%, Ta: 5.5%, Hf: 0.15%, Re : 1.4%, the balance being Ni.
[0034] Master alloy smelting: using high-purity metal components in a vacuum less than 1×10 -3 The alloy is smelted under the condition of Pa.
[0035] Preparation of nickel-based single crystal alloys: reducing the vacuum of the directional solidification furnace to 1×10 -3 Pa, the alloy is heated by electromagnetic induction, and the melting temperature of the alloy is kept at 1550°C for 15 minutes, poured into the prepared single crystal test rod mold, and pulled at a rate of 6mm / min to prepare a single crystal test rod.
[0036] Heat treatment of the single crystal test rod: solid solution temperature control: sequential heating to 1255°C for 2 hours, continued heating to 1265°C for 4 hours, and then heating to 1270°C for 2 hours;
[0037] Cool down to 1120°C for 4 hours for stabiliza...
Embodiment 2
[0040]The chemical composition weight percent of the designed alloy is: Cr: 9.6%, Co: 10.0%, Mo: 0.6%, W: 5.8%, Al: 4.5%, Ti: 3.15%, Ta: 5.5%, Hf: 0.14%, Re : 1.5%, the balance being Ni.
[0041] a. Master alloy smelting: use high-purity metal components in a vacuum less than 1×10 -3 The alloy is smelted under the condition of Pa.
[0042] b. Preparation of nickel-based single crystal alloy: reduce the vacuum of the directional solidification furnace to 1×10 -3 Pa, the alloy is heated by electromagnetic induction, the melting temperature of the alloy is kept at 1550°C for 25 minutes, poured into the prepared single crystal test rod mold, and pulled at a rate of 15mm / min to prepare a single crystal test rod.
[0043] c. Heat treatment of the single crystal test rod:
[0044] Solid solution temperature control: sequential heating to 1255°C for 2 hours, continued heating to 1265°C for 4 hours, and then heating to 1270°C for 2 hours.
[0045] Cool down to 1120°C for 4 hours fo...
Embodiment 3
[0048] The chemical composition weight percentage of the designed alloy is: Cr: 10.5%, Co: 9.5%, Mo: 1.0%, W: 5.62%, Al: 4.4%, Ti: 2.75%, Ta: 5.7%, Hf: 0.3%, Re : 1.7%, the balance being Ni.
[0049] a. Master alloy smelting: use high-purity metal components in a vacuum less than 1×10 -3 The alloy is smelted under the condition of Pa.
[0050] b. Preparation of nickel-based single crystal alloy: reduce the vacuum of the directional solidification furnace to 1×10 -3 Pa, the alloy is heated by electromagnetic induction, and the melting temperature of the alloy is kept at 1550°C for 30 minutes, poured into the prepared single crystal test rod mold, and pulled at a rate of 20mm / min to prepare a single crystal test rod.
[0051] c. Heat treatment of the single crystal test rod: solid solution temperature control: sequentially heating to 1255°C for 2 hours, continuing heating to 1265°C for 4 hours, then heating to 1270°C for 2 hours; cooling to 1120°C for 4 hours for stabilization...
PUM
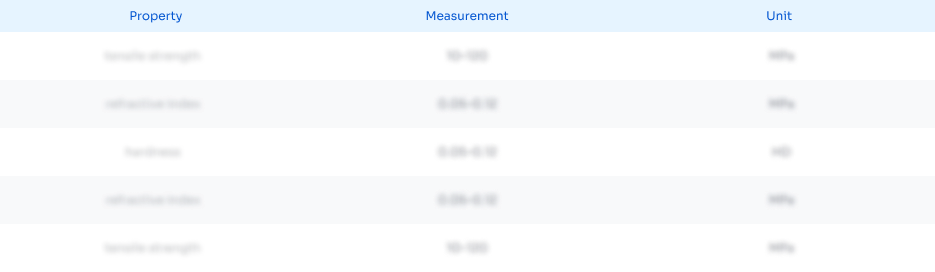
Abstract
Description
Claims
Application Information

- Generate Ideas
- Intellectual Property
- Life Sciences
- Materials
- Tech Scout
- Unparalleled Data Quality
- Higher Quality Content
- 60% Fewer Hallucinations
Browse by: Latest US Patents, China's latest patents, Technical Efficacy Thesaurus, Application Domain, Technology Topic, Popular Technical Reports.
© 2025 PatSnap. All rights reserved.Legal|Privacy policy|Modern Slavery Act Transparency Statement|Sitemap|About US| Contact US: help@patsnap.com