High-magnesium phosphate tailing enrichment and light calcium carbonate and magnesium hydroxide co-production method
A technology of light calcium carbonate and high-magnesium phosphorus tailings, which is applied in the treatment of phosphorus tailings, the treatment of high-magnesium phosphorus tailings and medium and low-grade phosphate rocks, the enrichment of high-magnesium phosphorus tailings and the co-production of magnesium hydroxide And food-grade light calcium carbonate field, to achieve the effect of good environmental benefits
- Summary
- Abstract
- Description
- Claims
- Application Information
AI Technical Summary
Problems solved by technology
Method used
Image
Examples
Embodiment 1
[0048] First, phosphate tailings are calcined at a temperature of 950-1000°C to form phosphate rock powder; the amount of phosphate rock powder in the leaching kettle is 5kg, and the amount of water added is 50L. After fully stirring, the pH value of the solution is about 10.5, and the heat of digestion The water temperature is 60°C, and the time is 1-2 hours; after hot water digestion, the secondary ammonium salt leaching is carried out; the feeding material for the first stage leaching ammonium chloride is 5 kg, the reaction time is 2 hours, and the second stage leaching of chlorine Feed 3kg of ammonium chloride, and the leaching time is also 2h. After the secondary leaching reaction, the two leaching solutions are combined to form a mixed leaching solution; the pH value of the mixed leaching solution is about 8.5. Then flush the mixed leaching solution into CO 2 Carry out carbonization reaction; CO in the carbonation reaction of mixed leaching solution 2 The concentration ...
Embodiment 2
[0054] First, the phosphorous tailings are calcined at a temperature of 950-1000°C to form phosphate rock powder; the amount of phosphate rock powder in the leaching kettle is 5kg, and the ammonium chloride mother liquor is recycled; after being digested by hot water at a temperature of 80°C, Carry out the secondary ammonium salt leaching, the temperature of the digested hot water is 80°C; add 0.5 kg of ammonium chloride during the first stage leaching, after fully stirring, the pH value of the solution is about 10.5, and the reaction time is 2 hours; Add 1 kg of ammonium chloride, and the leaching time is also 2 hours. After the secondary leaching reaction, the two leaching solutions are combined to form a mixed leaching solution; the pH value of the mixed leaching solution is about 8.8. Then flush the mixed leaching solution into CO 2 Carry out carbonization reaction; CO in the carbonation reaction of leaching solution 2 The concentration is 60%, the reaction temperature is...
Embodiment 3
[0058] First, the phosphorous tailings are calcined at a temperature of 950-1000°C to form phosphate rock powder; the amount of phosphate rock powder in the leaching kettle is 5kg, and the ammonium chloride mother liquor is recycled; after being digested by hot water at a temperature of 80°C, Add ammonium chloride 1.0kg during the first stage leaching. After fully stirring, the pH value of the solution is about 10.4, and the reaction time is 2h; After the extraction reaction is completed, the two leaching solutions are combined to form a mixed leaching solution; the pH value of the mixed leaching solution is about 8.5. Then flush the mixed leaching solution into CO 2 Carry out carbonization reaction; CO in the carbonation reaction of leaching solution 2 The concentration is 30%, the reaction temperature is controlled at 20-30°C, the carbonization reaction time is 60min, and the pH value at the end of the reaction is 7.5. The composition of the obtained phosphorus concentrate...
PUM
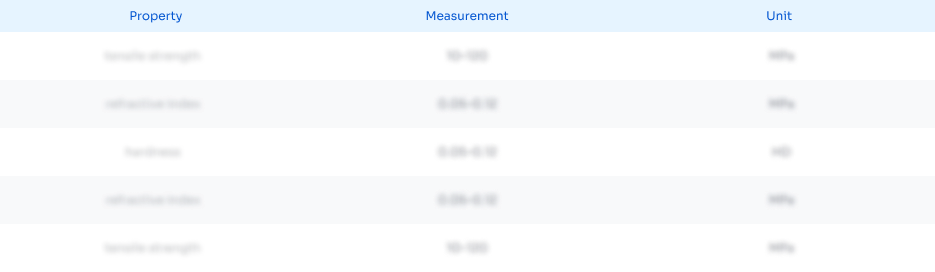
Abstract
Description
Claims
Application Information

- R&D
- Intellectual Property
- Life Sciences
- Materials
- Tech Scout
- Unparalleled Data Quality
- Higher Quality Content
- 60% Fewer Hallucinations
Browse by: Latest US Patents, China's latest patents, Technical Efficacy Thesaurus, Application Domain, Technology Topic, Popular Technical Reports.
© 2025 PatSnap. All rights reserved.Legal|Privacy policy|Modern Slavery Act Transparency Statement|Sitemap|About US| Contact US: help@patsnap.com