A cross-sectional design method of automobile body beam based on model validation technology
A design method and technology for body beams, applied in design optimization/simulation, calculation, special data processing applications, etc., to achieve the effect of shortening the design and processing cycle
- Summary
- Abstract
- Description
- Claims
- Application Information
AI Technical Summary
Problems solved by technology
Method used
Image
Examples
Embodiment 1
[0060] A specific embodiment of the present invention discloses a method for designing a body beam section based on model validation technology, such as figure 1 shown, including the following steps:
[0061] S1. Establish a physical model of the automobile body and obtain its corresponding body beam unit structure.
[0062] S2. According to the multi-objective optimization parameters and constraints, establish the body optimization objective function, obtain the optimal shape of the body beam section, the coordinates of key control points, and manufacture the corresponding body model. The establishment of the vehicle body optimization objective function aims to optimize the performance of the vehicle body and minimize the cost.
[0063] S3. Perform a static or dynamic load test on the vehicle body model in accordance with industrial design standards, and obtain actual measurement results of the vehicle body static or dynamic load test.
[0064] S4. Judging whether the above...
Embodiment 2
[0067] Optimizing on the basis of the above examples, such as figure 2 As shown, step S1 can be further refined into the following steps:
[0068] S11. According to preset requirements, a physical model of the vehicle body is established through modeling software. The physical model of the automobile body includes a body beam, a body skeleton structure, and the like.
[0069] S12. Carrying out finite element analysis on the physical model of the automobile body by means of finite element analysis method to obtain the corresponding body beam unit structure of the automobile.
[0070] S13. For each body beam unit structure, set initial model parameters. The initial model parameters include material parameters and wall thickness, wherein the material parameters include elastic modulus, Poisson's ratio, density and the like.
[0071] Preferably, in step S2, the multi-objective optimization parameters include body girder sectional area, y-axis moment of inertia, z-axis moment o...
PUM
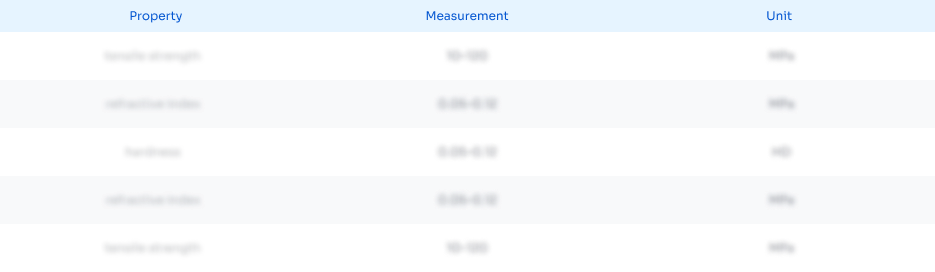
Abstract
Description
Claims
Application Information

- Generate Ideas
- Intellectual Property
- Life Sciences
- Materials
- Tech Scout
- Unparalleled Data Quality
- Higher Quality Content
- 60% Fewer Hallucinations
Browse by: Latest US Patents, China's latest patents, Technical Efficacy Thesaurus, Application Domain, Technology Topic, Popular Technical Reports.
© 2025 PatSnap. All rights reserved.Legal|Privacy policy|Modern Slavery Act Transparency Statement|Sitemap|About US| Contact US: help@patsnap.com