A co-shift process for methanol synthesis
A methanol synthesis and supporting technology, applied in hydrogen/synthesis gas production, chemical industry, indirect heat exchangers, etc., to achieve the effects of small resistance, increased control means, and mild operating environment
- Summary
- Abstract
- Description
- Claims
- Application Information
AI Technical Summary
Problems solved by technology
Method used
Image
Examples
Embodiment 2
[0077] Such as Figure 6 to Figure 9 As shown, in this embodiment, the first heat exchange tubes 41 and the second heat exchange tubes 42 are arranged in one-to-one correspondence. In this embodiment, the second heat exchange tube 42 is spirally wound on the first heat exchange tube 41, as Figure 9 As shown, the two are connected together by a tube clamp 43.
[0078] Each of the first heat exchange tubes 41 and the corresponding second heat exchange tubes 42 can also be arranged upright, and the corresponding two first heat exchange tubes and the second heat exchange tubes are positioned through a connecting piece; or, it can also be the first heat exchange tube A heat exchange tube is helically wound on the second heat exchange tube; or, two corresponding first heat exchange tubes and second heat exchange tubes may be helically wound together.
[0079] The inner diameter of the first heat exchange tube 41 is one-fifth of the inner diameter of the second heat exchange tube ...
PUM
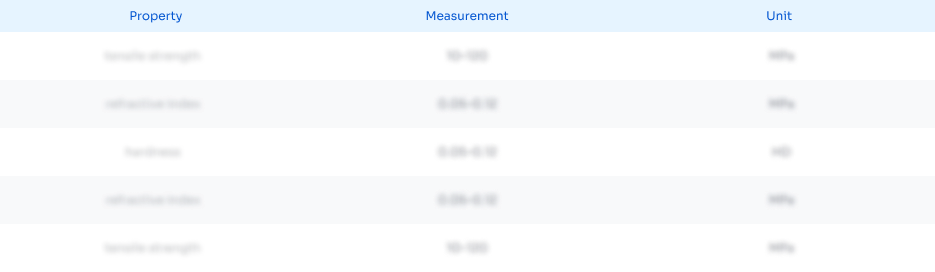
Abstract
Description
Claims
Application Information

- R&D
- Intellectual Property
- Life Sciences
- Materials
- Tech Scout
- Unparalleled Data Quality
- Higher Quality Content
- 60% Fewer Hallucinations
Browse by: Latest US Patents, China's latest patents, Technical Efficacy Thesaurus, Application Domain, Technology Topic, Popular Technical Reports.
© 2025 PatSnap. All rights reserved.Legal|Privacy policy|Modern Slavery Act Transparency Statement|Sitemap|About US| Contact US: help@patsnap.com