A kind of preparation method of insulating strip for solar module
A technology for solar modules and insulating strips is applied in the field of packaging materials, which can solve problems such as affecting the stability of modules and falling off glass, and achieve the effect of ensuring bonding force and good insulation performance.
- Summary
- Abstract
- Description
- Claims
- Application Information
AI Technical Summary
Problems solved by technology
Method used
Image
Examples
Embodiment 1
[0048] The first process:
[0049] (1) Substrate unwinding: release the milky white PET Mylar sheet film through the unwinding equipment;
[0050] (2) Apply high-frequency and high-voltage electricity to the corona treatment equipment to make it discharge to generate corona sparks;
[0051] (3) corona treatment is carried out to the inner side of the milky white PET mylar sheet film released in step 1 with the corona spark in step 2, so that the corona value of the treated surface reaches 52 dynes;
[0052] (4) the ethylene copolymer EVA resin particles are melted and casted by an extruder to form a transparent casting film;
[0053] (5) The corona-treated milky white PET Mylar sheet film in step 3 and the EVA cast film in step 4 pass through the composite equipment together. At this time, the EVA cast film and milky white PET Mylar sheet film were corona treated. Combination of one side, EVA cast film on the inside, and milky white PET Mylar film on the outside, to obtain c...
Embodiment 2
[0076] The first process:
[0077] (1) Substrate unwinding: release the milky white PET Mylar sheet film through the unwinding equipment;
[0078] (2) Apply high-frequency and high-voltage electricity to the corona treatment equipment to make it discharge to generate corona sparks;
[0079] (3) corona treatment is carried out to the inner side of the milky white PET mylar sheet film released in step 1 with the corona spark in step 2, so that the corona value of the treated surface reaches 52 dynes;
[0080] (4) the ethylene copolymer EVA resin particles are melted and casted by an extruder to form a transparent casting film;
[0081] (5) The corona-treated milky white PET Mylar sheet film in step 3 and the EVA cast film in step 4 pass through the composite equipment together. At this time, the EVA cast film and milky white PET Mylar sheet film were corona treated. Combination of one side, EVA cast film on the inside, and milky white PET Mylar film on the outside, to obtain c...
Embodiment 3
[0104] The first process:
[0105] (1) Substrate unwinding: release the milky white PET Mylar sheet film through the unwinding equipment;
[0106] (2) Apply high-frequency and high-voltage electricity to the corona treatment equipment to make it discharge to generate corona sparks;
[0107] (3) corona treatment is carried out to the inner side of the milky white PET mylar sheet film released in step 1 with the corona spark in step 2, so that the corona value of the treated surface reaches 52 dynes;
[0108] (4) the ethylene copolymer EVA resin particles are melted and casted by an extruder to form a transparent casting film;
[0109] (5) The corona-treated milky white PET Mylar sheet film in step 3 and the EVA cast film in step 4 pass through the composite equipment together. At this time, the EVA cast film and milky white PET Mylar sheet film were corona treated. Combination of one side, EVA cast film on the inside, and milky white PET Mylar film on the outside, to obtain c...
PUM
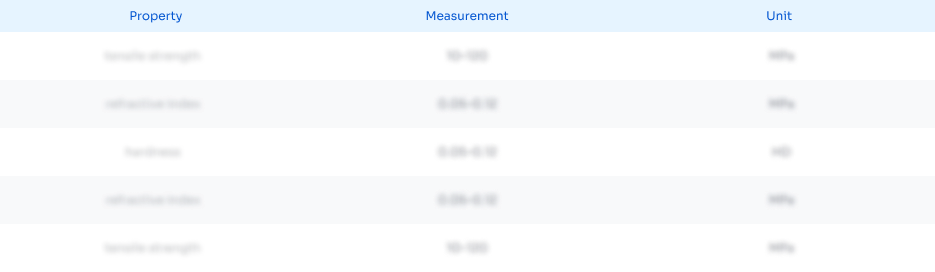
Abstract
Description
Claims
Application Information

- Generate Ideas
- Intellectual Property
- Life Sciences
- Materials
- Tech Scout
- Unparalleled Data Quality
- Higher Quality Content
- 60% Fewer Hallucinations
Browse by: Latest US Patents, China's latest patents, Technical Efficacy Thesaurus, Application Domain, Technology Topic, Popular Technical Reports.
© 2025 PatSnap. All rights reserved.Legal|Privacy policy|Modern Slavery Act Transparency Statement|Sitemap|About US| Contact US: help@patsnap.com