Hybrid four-gear transmission driving system
A hybrid power and drive system technology, applied in hybrid vehicles, power devices, pneumatic power devices, etc., can solve the problems of single end speed ratio of permanent magnet synchronous motors, poor driving comfort, and inability to shift gears, etc., to achieve convenience Design layout, good driving comfort, and the effect of eliminating impact
- Summary
- Abstract
- Description
- Claims
- Application Information
AI Technical Summary
Problems solved by technology
Method used
Image
Examples
Embodiment Construction
[0034] The present invention will be described in detail below in conjunction with specific embodiments shown in the accompanying drawings. However, these embodiments are not limited to the present invention, and structural, method, or functional changes made by those skilled in the art according to these embodiments are included within the protection scope of the present invention.
[0035] Such as figure 1 As shown, the present invention discloses a hybrid four-speed transmission drive system, including a differential 100, the final reduction gear 101 of the differential 100 can be driven by a hybrid drive assembly or / and a pure electric drive assembly, the The final reduction gear 101 of the differential 100 is connected to the hub of the vehicle.
[0036]In the present invention, the pure electric drive assembly at least includes a main drive motor 9 and a third output shaft 8 arranged on one side of the differential 100, and the motor shaft of the main drive motor 9 is f...
PUM
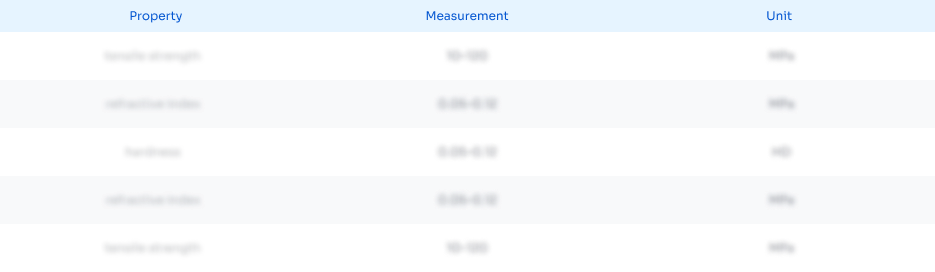
Abstract
Description
Claims
Application Information

- R&D
- Intellectual Property
- Life Sciences
- Materials
- Tech Scout
- Unparalleled Data Quality
- Higher Quality Content
- 60% Fewer Hallucinations
Browse by: Latest US Patents, China's latest patents, Technical Efficacy Thesaurus, Application Domain, Technology Topic, Popular Technical Reports.
© 2025 PatSnap. All rights reserved.Legal|Privacy policy|Modern Slavery Act Transparency Statement|Sitemap|About US| Contact US: help@patsnap.com