Method for preparing etherification catalyst and method for producing o-methylanisole
A catalyst and etherification technology, applied in the field of catalysis, can solve the problems of large hydrogen consumption, serious pollution, poor economy and the like, and achieve the effects of low preparation cost, simple production process and good stability
- Summary
- Abstract
- Description
- Claims
- Application Information
AI Technical Summary
Problems solved by technology
Method used
Image
Examples
preparation example Construction
[0036] Specifically, the present invention provides a kind of preparation method of etherification catalyst, described method comprises:
[0037] a) mixing the molecular sieve and the binder into shape and calcining at 500 to 700° C. for 4 to 10 hours;
[0038] c) modifying the product obtained in the previous step with an oxide and calcining at 550 to 700° C. for 3 to 10 hours, wherein the oxide is selected from one or more of alkaline earth metal oxides and transition metal oxides ;and
[0039] d) steaming the product obtained in the previous step at 300 to 800° C. for 0.5 to 10 hours,
[0040] Wherein the implementation order of step c) and step d) can be interchanged.
[0041] Preferably, the method further comprises the following step b) following step a):
[0042] b) The product obtained in step a) is subjected to acid treatment and calcined at 500 to 600° C. for 2 to 10 hours.
[0043] The molecular sieves selected according to the technical scheme of the present in...
Embodiment 1
[0062] The preparation process of the catalyst is as follows: 120 grams of HZSM-5 molecular sieves with a molar silicon-aluminum ratio of 20 are mixed with 60 grams of diatomaceous earth and 100 grams of silica sol containing 20% by weight of silicon dioxide, and an appropriate amount of 10% dilute Nitric acid is used as extrusion aid to extrude strips. Dry at 120°C and bake at 500°C for 10 hours. The above catalyst is cut into 1-3 mm to prepare columnar catalyst precursor A0. Add 20 grams of parent catalyst A0 to 50 ml of 10% nitric acid aqueous solution by weight, and soak at 30° C. for 4 hours. Dry at 120°C and bake at 550°C for 10 hours to prepare A1. 20 grams of A1 was steam treated for 10 hours in a 100% water vapor atmosphere, the treatment temperature was 550°C, and roasted at 550°C for 3 hours to obtain A2, and 20 grams of A2 samples were impregnated with a calcium nitrate aqueous solution with a concentration of 0.18% by weight After 24 hours, dry at 120° C., an...
Embodiment 2
[0064] The preparation process of the catalyst is as follows: 170 grams of HZSM-5 molecular sieve with a molar silicon-aluminum ratio of 30 is mixed with 100 g of silica sol containing 30% by weight of silicon dioxide, and an appropriate amount of 10% dilute nitric acid is added as an extrusion aid to extrude forming. Dry at 120°C and bake at 700°C for 4 hours. The above catalyst is cut into 1-3 mm to prepare columnar catalyst precursor B0. 20 grams of parent catalyst B0 was added to 50 ml of 10% nitric acid aqueous solution by weight, and soaked at 30° C. for 10 hours. Dry at 120°C, and then bake at 800°C for 2 hours to prepare B1. 20 grams of the B1 sample was immersed in an aqueous solution of barium nitrate with a concentration of 1% by weight for 12 hours, dried at 120° C., and roasted at 550° C. for 10 hours. The weight content of barium oxide was 1% to obtain B2. Catalyst B was obtained by steaming 20 grams of B2 in a 100% steam atmosphere for 0.5 hour at a temperatu...
PUM
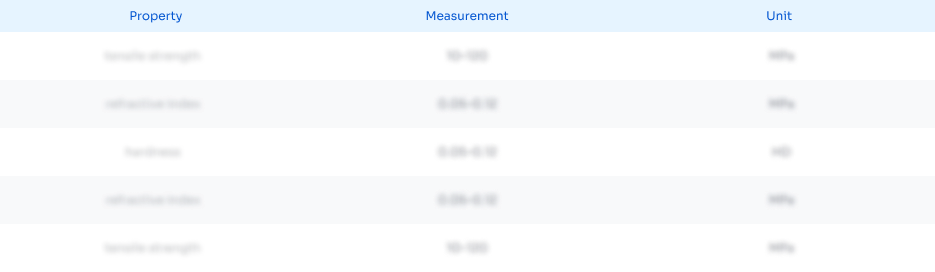
Abstract
Description
Claims
Application Information

- R&D Engineer
- R&D Manager
- IP Professional
- Industry Leading Data Capabilities
- Powerful AI technology
- Patent DNA Extraction
Browse by: Latest US Patents, China's latest patents, Technical Efficacy Thesaurus, Application Domain, Technology Topic, Popular Technical Reports.
© 2024 PatSnap. All rights reserved.Legal|Privacy policy|Modern Slavery Act Transparency Statement|Sitemap|About US| Contact US: help@patsnap.com