A kind of preparation method of graphene coated porous material
A graphene-coated, porous material technology, applied in the direction of structural parts, electrical components, battery electrodes, etc., can solve the problems of complex preparation process and lack of broad spectrum, achieve uniform pore size distribution, easy large-scale production, process stable effect
- Summary
- Abstract
- Description
- Claims
- Application Information
AI Technical Summary
Problems solved by technology
Method used
Image
Examples
Embodiment 1
[0044] A preparation method of graphene-coated porous material: take 0.1g graphene oxide and 1gZnSb alloy material, mix them evenly, hang them in a vacuum heat treatment furnace (model: OTF-1200X-S-II, MTI), and keep them warm at 500°C After 2 hours, the vacuum degree was set to 10 Pa to obtain graphene-coated porous antimony.
Embodiment 2
[0046] A kind of preparation method of graphene-coated porous material: get 0.1g graphene oxide and 2gZn 2 Sb 3 The materials were mixed evenly and suspended in a vacuum heat treatment furnace (model: OTF-1200X-S-II, MTI), kept at 600°C for 1 hour, and the vacuum degree was set to 8Pa to obtain graphene-coated porous antimony.
Embodiment 3
[0048] A kind of preparation method of graphene-coated porous material: get 0.1g graphene oxide and 1gAlZn material, mix uniformly, hang in laboratory small vacuum heat treatment furnace (model: OTF-1200X-S-II, MTI), in 300 ℃ for 2 hours, and the vacuum degree is set to 9Pa to obtain graphene-composite porous aluminum.
PUM
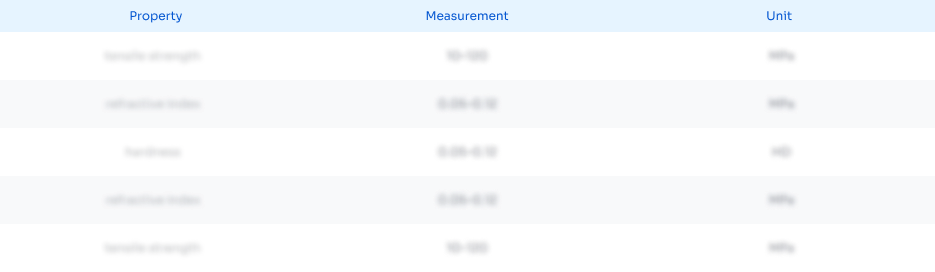
Abstract
Description
Claims
Application Information

- R&D Engineer
- R&D Manager
- IP Professional
- Industry Leading Data Capabilities
- Powerful AI technology
- Patent DNA Extraction
Browse by: Latest US Patents, China's latest patents, Technical Efficacy Thesaurus, Application Domain, Technology Topic, Popular Technical Reports.
© 2024 PatSnap. All rights reserved.Legal|Privacy policy|Modern Slavery Act Transparency Statement|Sitemap|About US| Contact US: help@patsnap.com