A safety design method for water tank used in airtightness test of aeroengine casing
A technology for aero-engine and safety design, applied in the direction of design optimization/simulation, calculation, special data processing applications, etc., can solve problems such as lack of physical meaning, complex equation form, difficult to popularize and apply, etc., to achieve a reasonable and solid theoretical foundation, clear physical Meaning, concise and clear effect
Active Publication Date: 2019-01-22
NANCHANG HANGKONG UNIVERSITY
View PDF2 Cites 4 Cited by
- Summary
- Abstract
- Description
- Claims
- Application Information
AI Technical Summary
Problems solved by technology
In fact, for different fields and technical characteristics, the performance requirements for airtight test devices are also different, so it is difficult to have an airtight device design method suitable for all pressure vessels
At the same time, there is a lack of rich technical references for the safety design method of the aero-engine case air-tightness test device. The traditional design method of the aero-engine case air-tightness test water tank and other devices can no longer meet the requirements of the current aero-engine machine. The requirements for resisting the risk of sudden debris impact under the experimental conditions of the airtightness of the tank, and the traditional airtight water tank design methods have not fully considered the existence of plugs of different shapes, sizes and masses at different flight speeds and scattering angles. Effects of flying out and other conditions on the impact kinetic energy and impact force of plug fragments
Some design schemes of pressure vessel airtightness test devices have certain physical principles and a relatively mature theoretical system, but due to the complex form of equations, numerous material parameters and even cross-scale values, the parameter optimization and fitting procedures are cumbersome, and it is not easy to obtain accurate results. technical parameters, which reduces the prediction accuracy and is not suitable for engineering applications
In addition, some design schemes are based on the macroscopic phenomenological method. Although the model form is simple and the relevant parameters are easy to obtain, it lacks clear physical meaning, and the basic theory supporting the method research is not perfect, so it is difficult to popularize and apply.
Method used
the structure of the environmentally friendly knitted fabric provided by the present invention; figure 2 Flow chart of the yarn wrapping machine for environmentally friendly knitted fabrics and storage devices; image 3 Is the parameter map of the yarn covering machine
View moreImage
Smart Image Click on the blue labels to locate them in the text.
Smart ImageViewing Examples
Examples
Experimental program
Comparison scheme
Effect test
example
[0040] Example: Water tank safety design method for casing airtightness test in an aero-engine
[0041] Step S1, carry out the modeling and solving of the plug separation initial velocity.
the structure of the environmentally friendly knitted fabric provided by the present invention; figure 2 Flow chart of the yarn wrapping machine for environmentally friendly knitted fabrics and storage devices; image 3 Is the parameter map of the yarn covering machine
Login to View More PUM
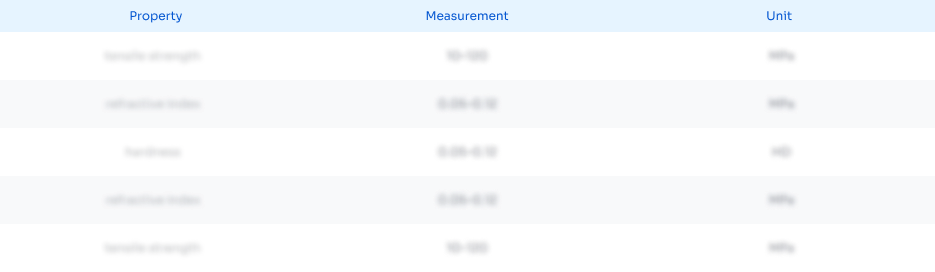
Abstract
A safety design method for water tank used in airtightness test of aeroengine casing is disclosed. Based on the relevant technical parameters of the water tank and the machine case with specific requirements, By using the equations of motion and gas state, combining with dimensionless time and pressure and initial conditions, the second order differential equations of dimensionless pressure and flight angle of plug fracture are established, the differential equations can be used to calculate different internal pressures, the initial and angular velocities of the plug fragment as it exits at the debris size, and then the mechanics equation is established by using the fluid mechanics principle, a method for calculating the impact velocity of plug considering the resistance coefficient of medium is established, the theorem of kinetic energy and the law of conservation of energy are used to model and estimate the wall thickness of water tank, the impact force of plug fragment and the impact strength of fragment. In order to meet the needs of engineering calculation, a conservative formula for calculating the initial velocity of plug separation is established. Finally, the safety designscheme of water tank for aero-engine casing airtightness test which meets the technical requirements can be obtained.
Description
technical field [0001] The present invention relates to the field of water tank safety design for aero-engine casing air tightness test, and in particular to a kind of air tightness test of a high-pressure container, in order to resist the breakage and impact of plugs, plugs or connectors. Impact force, the calculation method of the structural thickness and strength of each work area to ensure the safety of the water tank. Background technique [0002] High pressure vessels are defined as airtight vessels subject to high fluid pressure, and are widely used in petrochemical industry, energy industry, aerospace, scientific research and military industry and other fields. With the development of aero-engine technology, sealing performance has become an important factor affecting engine performance and life. During the service period, the aero-engine casing is the main component that forms the airflow channel, load bearing and transmission. However, due to manufacturing proces...
Claims
the structure of the environmentally friendly knitted fabric provided by the present invention; figure 2 Flow chart of the yarn wrapping machine for environmentally friendly knitted fabrics and storage devices; image 3 Is the parameter map of the yarn covering machine
Login to View More Application Information
Patent Timeline

Patent Type & Authority Applications(China)
IPC IPC(8): G06F17/50
CPCG06F30/20
Inventor 胡晓安薛志远周超刘建谋杨晓光
Owner NANCHANG HANGKONG UNIVERSITY
Features
- Generate Ideas
- Intellectual Property
- Life Sciences
- Materials
- Tech Scout
Why Patsnap Eureka
- Unparalleled Data Quality
- Higher Quality Content
- 60% Fewer Hallucinations
Social media
Patsnap Eureka Blog
Learn More Browse by: Latest US Patents, China's latest patents, Technical Efficacy Thesaurus, Application Domain, Technology Topic, Popular Technical Reports.
© 2025 PatSnap. All rights reserved.Legal|Privacy policy|Modern Slavery Act Transparency Statement|Sitemap|About US| Contact US: help@patsnap.com