Aluminum-plastic plate and composite processing technology thereof
A technology of composite processing and aluminum-plastic panels, applied in the field of building decoration materials, can solve problems such as protection, scratching, and damage that are difficult to achieve, achieve stable anti-radiation, improve anti-radiation function, and avoid the effects of no longer strong bonding
- Summary
- Abstract
- Description
- Claims
- Application Information
AI Technical Summary
Problems solved by technology
Method used
Examples
Embodiment 1
[0032] This embodiment relates to an aluminum-plastic panel, including an upper aluminum alloy plate, a base plate and a lower aluminum alloy plate, the base plate is located between the upper aluminum alloy plate and the lower aluminum alloy plate, and between the upper aluminum alloy plate, the base plate and the lower aluminum alloy plate All are compounded by a polymer adhesive film, and the polymer adhesive film used in this embodiment is a polyethylene film. And the outer surface of the upper aluminum alloy plate is coated with a fluorocarbon resin coating, and the outer surface of the lower aluminum alloy plate is coated with a polyester coating. The intermediate substrate is composed of the following weight components: 92.8kg polyethylene, 16kg maleic anhydride grafted polyethylene, 1.6kg nano-zinc oxide, 0.16kg dicumyl peroxide, 0.16 triallyl isocyanide Uric acid ester and 24kg of boron carbide micropowder.
[0033] The composite processing technology adopted by the ...
Embodiment 2
[0039] The main difference between this embodiment and Embodiment 1 is that the polymer adhesive film used in this embodiment is an ethylene-vinyl acetate copolymer film, and the substrate of this embodiment is composed of the following components: 90kg of polyethylene, 18kg of polyethylene Maleic anhydride grafted polyethylene, 2.25 kg of nano-zinc oxide, 0.15 kg of dicumyl peroxide, 0.45 of triallyl isocyanurate and 27 kg of boron carbide micropowder.
[0040] In the composite processing process of this embodiment, the stirring speed of the raw materials of the substrate in the mixer is 400 r / min, the stirring time is 4 min, and the extrusion speed of the extruder is 4 m / min; the hot pressing temperature of the aluminum-plastic composite machine is 196±1℃.
Embodiment 3
[0042] The main difference between this embodiment and the first embodiment is that the polymer adhesive film used in this embodiment is a polypropylene film, and the substrate of this embodiment is composed of the following components: 78 kg of polyethylene, 16.8 kg of maleic anhydride Grafted polyethylene, 2.4 kg of nano-zinc oxide, 0.18 kg of dicumyl peroxide, 0.18 of triallyl isocyanurate and 24 kg of boron carbide micropowder.
[0043] In the composite processing process of this embodiment, the stirring speed of the raw materials of the substrate in the mixer is 500 r / min, the stirring time is 2 min, and the extrusion speed of the extruder is 5 m / min; the hot pressing temperature of the aluminum-plastic composite machine is 204±1℃.
PUM
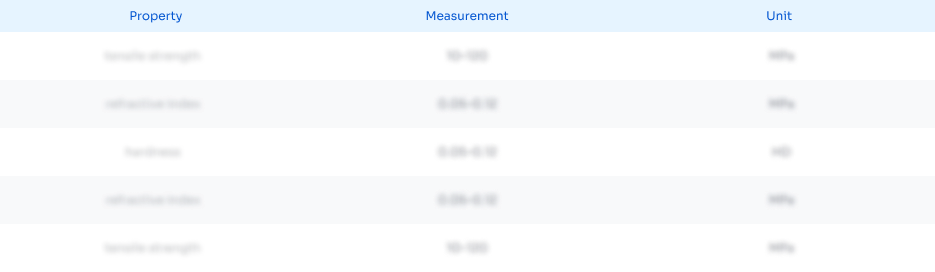
Abstract
Description
Claims
Application Information

- R&D Engineer
- R&D Manager
- IP Professional
- Industry Leading Data Capabilities
- Powerful AI technology
- Patent DNA Extraction
Browse by: Latest US Patents, China's latest patents, Technical Efficacy Thesaurus, Application Domain, Technology Topic, Popular Technical Reports.
© 2024 PatSnap. All rights reserved.Legal|Privacy policy|Modern Slavery Act Transparency Statement|Sitemap|About US| Contact US: help@patsnap.com