Rivet welding process of sheet material
A riveting and plate technology, applied in the direction of manufacturing tools, welding equipment, auxiliary welding equipment, etc., can solve the problems of easy cracks and low welding efficiency, and achieve the effect of reducing usage, improving welding effect, and welding firmness
- Summary
- Abstract
- Description
- Claims
- Application Information
AI Technical Summary
Problems solved by technology
Method used
Image
Examples
Embodiment Construction
[0025] The technical solutions in the embodiments of the present invention will be clearly and completely described below in conjunction with the accompanying drawings in the embodiments of the present invention. Obviously, the described embodiments are only a part of the embodiments of the present invention, rather than all the embodiments.
[0026] Reference figure 1 , A riveting welding process for plates, including the following steps:
[0027] S1: Sheet forming, cutting, bending, grinding and shot blasting the sheet to obtain the parts of the work piece, and rivet holes are opened on the parts of the work piece;
[0028] S2: Count the workpieces, check the parts and accessories that need to be riveted, and store them separately;
[0029] S3: Make assembly welding tooling, and make suitable assembly welding tooling according to the size of workpiece accessories;
[0030] S4: Align the rivet holes, assemble the workpiece through the welding tooling, and rivet the holes;
[0031] S5: ...
PUM
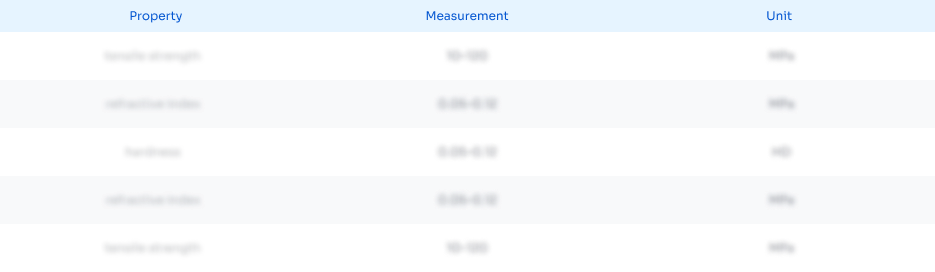
Abstract
Description
Claims
Application Information

- Generate Ideas
- Intellectual Property
- Life Sciences
- Materials
- Tech Scout
- Unparalleled Data Quality
- Higher Quality Content
- 60% Fewer Hallucinations
Browse by: Latest US Patents, China's latest patents, Technical Efficacy Thesaurus, Application Domain, Technology Topic, Popular Technical Reports.
© 2025 PatSnap. All rights reserved.Legal|Privacy policy|Modern Slavery Act Transparency Statement|Sitemap|About US| Contact US: help@patsnap.com