A method of electrolytic plating power supply
An electrolytic electroplating and power supply technology, applied in the modification of power electronics, electrical components, and output power conversion devices, etc., can solve the problems of damage to the power supply group, affecting the quality of electroplating, failure to achieve anti-corrosion, etc., and achieve stable internal current. Convenient control and detection to ensure the effect of normal operation
- Summary
- Abstract
- Description
- Claims
- Application Information
AI Technical Summary
Problems solved by technology
Method used
Image
Examples
Embodiment Construction
[0025] The following will clearly and completely describe the technical solutions in the embodiments of the present invention with reference to the accompanying drawings in the embodiments of the present invention. Obviously, the described embodiments are only some, not all, embodiments of the present invention. Based on the embodiments of the present invention, all other embodiments obtained by persons of ordinary skill in the art without making creative efforts belong to the protection scope of the present invention.
[0026] see Figure 1~3, a method for electrolytic plating power supply, comprising a main box 1, a coolant 2, an information processor 3, a signal switch 4, a current detection port 5, a cooling fan 6, a voltage detection port 7, a voltage regulator 8, an output port 9. Current regulation component 10, ventilation heat sink 11, electronic touch screen 12, safety signal light 13, insulating handle 14, electrolytic tank 15, rectifier circuit 16, unijunction tran...
PUM
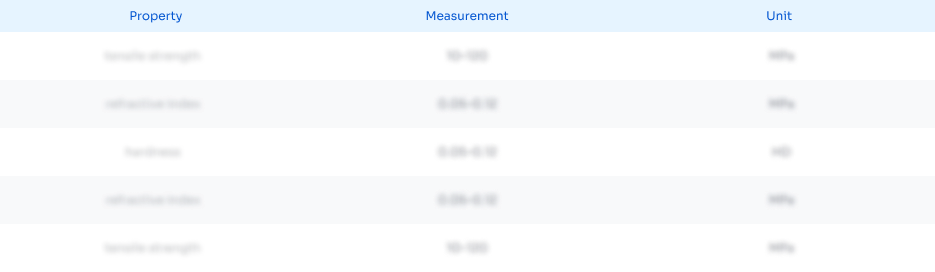
Abstract
Description
Claims
Application Information

- Generate Ideas
- Intellectual Property
- Life Sciences
- Materials
- Tech Scout
- Unparalleled Data Quality
- Higher Quality Content
- 60% Fewer Hallucinations
Browse by: Latest US Patents, China's latest patents, Technical Efficacy Thesaurus, Application Domain, Technology Topic, Popular Technical Reports.
© 2025 PatSnap. All rights reserved.Legal|Privacy policy|Modern Slavery Act Transparency Statement|Sitemap|About US| Contact US: help@patsnap.com