A kind of manufacturing method of solid capacitor
A manufacturing method and capacitor technology, which is applied in the direction of electrolytic capacitor manufacturing, capacitors, electrolytic capacitors, etc., can solve problems affecting product consistency, many production process steps, and long product production cycles, so as to reduce ESR series equivalent resistance and reduce The effect of absorbing water and being contaminated by impurities and reducing the exposure time
- Summary
- Abstract
- Description
- Claims
- Application Information
AI Technical Summary
Problems solved by technology
Method used
Examples
Embodiment 1
[0072] A method for manufacturing a solid capacitor, the steps are as follows:
[0073] S1. Cutting, cutting the positive electrode foil, negative electrode foil and electrolytic paper into a set width; nailing the positive electrode guide pin to the positive electrode foil, nailing the negative electrode guide pin to the negative electrode foil, and nailing the electrolytic paper to the positive electrode foil and negative electrode foil Stacking, the electrolytic paper is interposed between the positive electrode foil and the negative electrode foil, and the positive electrode foil, the negative electrode foil and the electrolytic paper are wound together into a core package; each core package is numbered by laser printing;
[0074] S2. Detect whether the core packs are short-circuited one by one, and immerse the qualified core packs in the chemical solution for chemical repair; wherein, in the chemical repair process, the positive and negative guide pins of the core pack are...
PUM
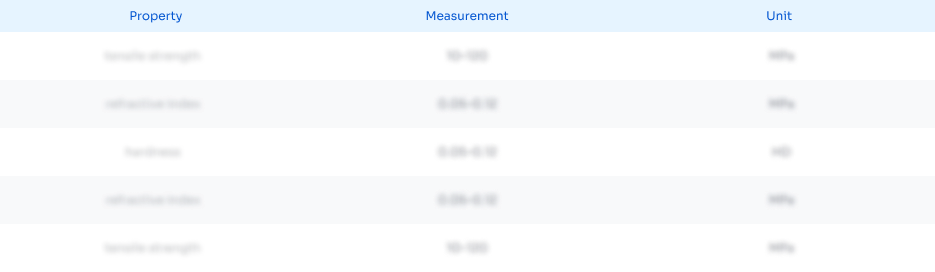
Abstract
Description
Claims
Application Information

- Generate Ideas
- Intellectual Property
- Life Sciences
- Materials
- Tech Scout
- Unparalleled Data Quality
- Higher Quality Content
- 60% Fewer Hallucinations
Browse by: Latest US Patents, China's latest patents, Technical Efficacy Thesaurus, Application Domain, Technology Topic, Popular Technical Reports.
© 2025 PatSnap. All rights reserved.Legal|Privacy policy|Modern Slavery Act Transparency Statement|Sitemap|About US| Contact US: help@patsnap.com