High temperature-resisting active coating and preparation method thereof
An active coating, high temperature resistant technology, applied in catalyst activation/preparation, chemical instruments and methods, metal/metal oxide/metal hydroxide catalysts, etc. problems such as low rate, to achieve the effect of simple method, easy operation and good heat resistance stability
- Summary
- Abstract
- Description
- Claims
- Application Information
AI Technical Summary
Problems solved by technology
Method used
Image
Examples
Embodiment 1
[0031] (1) Take 5.0 grams of pseudoboehmite, 44 grams of γ-Al 2 o3 , 44 grams of Ce-Zr composite oxide, 1.25 grams of PEG6000, add 100 grams of deionized water and mix evenly;
[0032] (2) Take 8.4 grams of cerium nitrate, 0.35 grams of lanthanum nitrate, 5 grams of 7% polyvinyl alcohol aqueous solution, 2.0 grams of urea, add 50 grams of deionized water to dissolve and mix;
[0033] Mix the above two coating materials and stir evenly at high speed, slowly add 20.0 grams of SiO 2 Silica sol with a mass percentage of 22% and an average particle size of 15nm was moved to a ball mill jar and ball milled at a frequency of 30Hz for 16h to obtain a slurry, and then added HNO 3 Adjust the pH of the slurry to 3.5.
[0034] (3) Immerse the blank honeycomb ceramic carrier in the coating slurry for 2 minutes, take it out and blow it with compressed air to remove the excess slurry in the channels, then dry it at 50°C for 2h, at 120°C for 2h, and bake it at 600°C for 3h. The product is ...
Embodiment 2
[0036] (1) Take 6.0 grams of pseudo-boehmite, 44 grams of γ-Al 2 o 3 , 44 grams of Ce-Zr-Al composite oxide, 2.0 grams of PEG8000, add 100 grams of deionized water and mix evenly;
[0037] (2) Take 8.0 grams of cerium nitrate, 0.40 grams of lanthanum nitrate, 0.40 grams of praseodymium nitrate, add 50 grams of deionized water to dissolve and mix;
[0038] Mix the above two coating materials and stir evenly at high speed, slowly add 20.0 grams of SiO 2 Silica sol with a mass percentage of 21% and an average particle size of 17nm was moved to a ball mill jar and milled at a frequency of 30Hz for 16h to obtain a slurry, and then HNO was added 3 Adjust the pH of the slurry to 3.7.
[0039] (3) Immerse the blank honeycomb ceramic carrier in the coating slurry for 2 minutes, take it out and blow it with compressed air to remove the excess slurry in the channels, then dry it at 60°C for 2h, at 110°C for 4h, and bake it at 600°C for 3h. The product is labeled B.
Embodiment 3
[0041] (1) Take 6.0 grams of pseudo-boehmite, 44 grams of γ-Al 2 o 3 , 44 grams of Ce-Zr-Pr composite oxide, 1.5 grams of PEG5000, add 100 grams of deionized water and mix evenly;
[0042] (2) Take 8.4 grams of cerium nitrate, 0.35 grams of lanthanum nitrate, 4.5 grams of 7% polyvinyl alcohol aqueous solution, 2.0 grams of urea, add 50 grams of deionized water to dissolve and mix;
[0043] Mix the above two coating materials and stir evenly at high speed, slowly add 20.0 grams of SiO 2 Silica sol with a mass percentage of 22% and an average particle size of 15nm was moved to a ball mill jar and ball milled at a frequency of 30Hz for 16h to obtain a slurry, and then added HNO 3 Adjust the pH of the slurry to 3.6.
[0044] (3) Immerse the blank honeycomb ceramic carrier in the coating slurry for 2 minutes, take it out and blow it with compressed air to remove the excess slurry in the channels, then dry it at 60°C for 4 hours, at 110°C for 2 hours, and bake it at 700°C for 2 h...
PUM
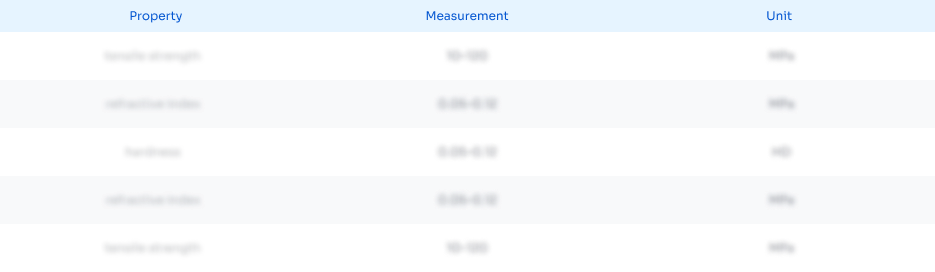
Abstract
Description
Claims
Application Information

- R&D Engineer
- R&D Manager
- IP Professional
- Industry Leading Data Capabilities
- Powerful AI technology
- Patent DNA Extraction
Browse by: Latest US Patents, China's latest patents, Technical Efficacy Thesaurus, Application Domain, Technology Topic, Popular Technical Reports.
© 2024 PatSnap. All rights reserved.Legal|Privacy policy|Modern Slavery Act Transparency Statement|Sitemap|About US| Contact US: help@patsnap.com