A kind of nylon yarn production process
A production process and technology of nylon yarn, which is applied in the field of nylon production, can solve the problems of unfavorable long-term storage of nylon yarn, uneven drying degree of nylon, high local temperature, etc., and achieve the effect of improving drying efficiency, uniform drying and reducing heat loss
- Summary
- Abstract
- Description
- Claims
- Application Information
AI Technical Summary
Problems solved by technology
Method used
Image
Examples
Embodiment approach
[0038] As an embodiment of the present invention, a semi-cylindrical barrel 71 is provided below the mesh plate 7; the semi-cylindrical barrel 71 is fixedly connected to the mesh plate 7, and a Through holes, a corrugated tube 72 is provided below the semi-cylindrical tube 71; the corrugated tube 72 is made of heat insulating material, the upper end of the corrugated tube 72 is fixedly connected with the cylindrical surface of the semi-cylindrical tube 71, and the lower end of the corrugated tube 72 is connected to the shell 1, and each corrugated tube 72 is connected to a secondary air intake hole; when in use, the hot air passing through the main air intake hole quickly enters the corrugated tube 72 through the secondary air intake hole, and then passes through the semi-cylindrical tube 71 at the upper end Evenly dispersed on the mesh plate 7, the hot air reduces the loss of heat during the transfer process, on the one hand, it improves the drying efficiency, and on the other...
PUM
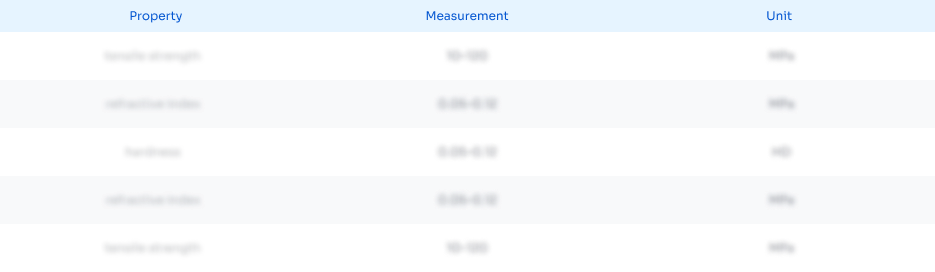
Abstract
Description
Claims
Application Information

- R&D Engineer
- R&D Manager
- IP Professional
- Industry Leading Data Capabilities
- Powerful AI technology
- Patent DNA Extraction
Browse by: Latest US Patents, China's latest patents, Technical Efficacy Thesaurus, Application Domain, Technology Topic, Popular Technical Reports.
© 2024 PatSnap. All rights reserved.Legal|Privacy policy|Modern Slavery Act Transparency Statement|Sitemap|About US| Contact US: help@patsnap.com