Solvent recovery method for para-aramid fiber production
A technology of para-aramid fibers and recycling methods, applied in the direction of organic chemistry, etc., to reduce the risk of decomposition, reduce the decomposition rate, and improve the recovery rate
- Summary
- Abstract
- Description
- Claims
- Application Information
AI Technical Summary
Problems solved by technology
Method used
Image
Examples
Embodiment 1
[0030] Use calcium carbonate to neutralize the washing solution after PPTA polymerization until the pH reaches about 6. Then the neutralized washing liquid is transported to the extraction tower for extraction and separation, and the extraction agent is chloroform. The extraction phase extracted from the bottom of the extraction tower is sent to the rough division section for the separation of extractant and NMP. The main equipment of the rough division is two falling film evaporators. The primary evaporator maintains the operating temperature at around 60°C and the vacuum at around -0.06MPa. The operating temperature of the secondary evaporator is kept at about 80°C, and the vacuum degree is kept at about -0.07MPa. Chloroform is extracted from the top of the two evaporators, and crude fraction material is extracted from the bottom. The content of extractant in the coarse material is about 10%; the coarse material is sent to the fine separation section to further separate t...
Embodiment 2
[0033] Use calcium carbonate to neutralize the washing solution after PPTA polymerization until the pH reaches about 6. Then the neutralized washing liquid is transported to the extraction tower for extraction and separation, and the extraction agent is chloroform. The extraction phase extracted from the bottom of the extraction tower is sent to the rough division section for the separation of extractant and NMP. The main equipment of coarse separation is a falling film evaporator. The primary evaporator maintains an operating temperature of around 80°C and a vacuum of around -0.06MPa. Chloroform is extracted from the top of the evaporator, and the crude material is extracted from the bottom. The content of extractant in the coarse material is about 15%; the coarse material is sent to the fine separation section to further separate the extractant. The fine separation equipment adopts a rectification tower. Before entering the rectification tower, 8% hot water with a temper...
Embodiment 3
[0035] Use calcium carbonate to neutralize the washing solution after PPTA polymerization until the pH reaches about 6. Then the neutralized washing liquid is transported to the extraction tower for extraction and separation, and the extraction agent is chloroform. The extraction phase extracted from the bottom of the extraction tower is sent to the rough division section for the separation of extractant and NMP. The main equipment of coarse fractionation is a plate distillation column. The operating temperature of the distillation tower is kept at about 70°C, and the vacuum degree is kept at about -0.06MPa. Chloroform is extracted from the top of the evaporator, and the crude material is extracted from the bottom. The content of extractant in the coarse material is about 10%; the coarse material is sent to the fine separation section to further separate the extractant. The fine separation equipment adopts a rectification tower. Before entering the rectification tower, 2% ...
PUM
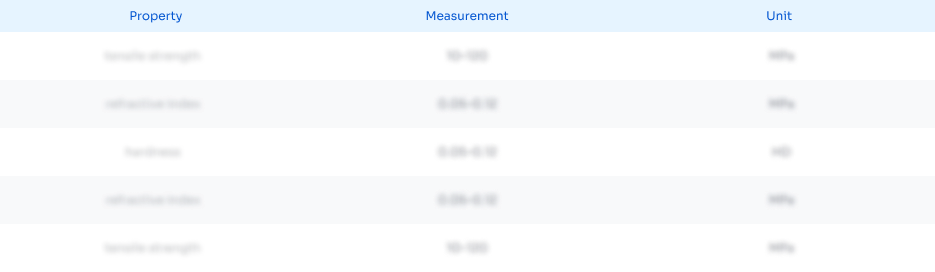
Abstract
Description
Claims
Application Information

- R&D Engineer
- R&D Manager
- IP Professional
- Industry Leading Data Capabilities
- Powerful AI technology
- Patent DNA Extraction
Browse by: Latest US Patents, China's latest patents, Technical Efficacy Thesaurus, Application Domain, Technology Topic, Popular Technical Reports.
© 2024 PatSnap. All rights reserved.Legal|Privacy policy|Modern Slavery Act Transparency Statement|Sitemap|About US| Contact US: help@patsnap.com