A method for preparing polycarbonate/graphene superhydrophobic porous membrane by 3D printing
A polycarbonate, 3D printing technology, applied in the direction of separation methods, chemical instruments and methods, membranes, etc., can solve the problems of poor mechanical stability of porous membranes, difficulty in controlling the formation of membrane pores, and the need to improve hydrophobicity, so as to improve compatibility Sexuality, uniform and orderly distribution, and the effect of improving mechanical strength and deformability
- Summary
- Abstract
- Description
- Claims
- Application Information
AI Technical Summary
Problems solved by technology
Method used
Image
Examples
Embodiment 1
[0034] (1) Add graphene powder and cross-linking agent into deionized water, disperse evenly, then place in a closed container, pass fluorine gas under high temperature and stirring state, cool and discharge the material after the reaction is completed, and obtain fluorinated graphene Hydrogel; the crosslinking agent is ethylenediamine; the parts by weight of each raw material are 16 parts by weight of graphene powder, 2 parts by weight of crosslinking agent, 75 parts by weight of deionized water, and 7 parts by weight of fluorine gas;
[0035] (2) Vacuum freeze-dry the hydrogel prepared in step (1) to obtain airgel, and then grind it into a powder with an average particle size of 90nm to obtain fluorinated graphene airgel powder; the vacuum freeze-dried The temperature is 5Pa, the temperature is -46℃, and the time is 25h;
[0036] (3) Heat the polycarbonate to melt, add the fluorinated graphene airgel powder, antioxidant and lubricant prepared in step (2), disperse evenly, an...
Embodiment 2
[0040] (1) Add graphene powder and cross-linking agent into deionized water, disperse evenly, then place in a closed container, pass fluorine gas under high temperature and stirring state, cool and discharge the material after the reaction is completed, and obtain fluorinated graphene Hydrogel; the crosslinking agent is polyethyleneimine; the parts by weight of each raw material are 13 parts by weight of graphene powder, 1 part by weight of crosslinking agent, 80 parts by weight of deionized water, and 6 parts by weight of fluorine gas;
[0041] (2) Vacuum freeze-dry the hydrogel prepared in step (1) to obtain airgel, and then grind it into a powder with an average particle size of 100nm to obtain fluorinated graphene airgel powder; the vacuum freeze-dried The temperature is 5Pa, the temperature is -42℃, and the time is 27h;
[0042] (3) Heat the polycarbonate to melt, add the fluorinated graphene airgel powder, antioxidant and lubricant prepared in step (2), disperse evenly, ...
Embodiment 3
[0046] (1) Add graphene powder and cross-linking agent into deionized water, disperse evenly, then place in a closed container, pass fluorine gas under high temperature and stirring state, cool and discharge the material after the reaction is completed, and obtain fluorinated graphene Hydrogel; cross-linking agent is polydiallyl dimethyl ammonium chloride; parts by weight of each raw material are 16 parts by weight of graphene powder, 3 parts by weight of cross-linking agent, 73 parts by weight of deionized water, fluorine gas 8 parts by weight;
[0047] (2) Vacuum freeze-dry the hydrogel prepared in step (1) to obtain airgel, and then grind it into a powder with an average particle size of 80nm to obtain fluorinated graphene airgel powder; the vacuum freeze-dried The temperature is 5Pa, the temperature is -42℃, and the time is 25h;
[0048] (3) Heat the polycarbonate to melt, add the fluorinated graphene airgel powder, antioxidant and lubricant prepared in step (2), disperse...
PUM
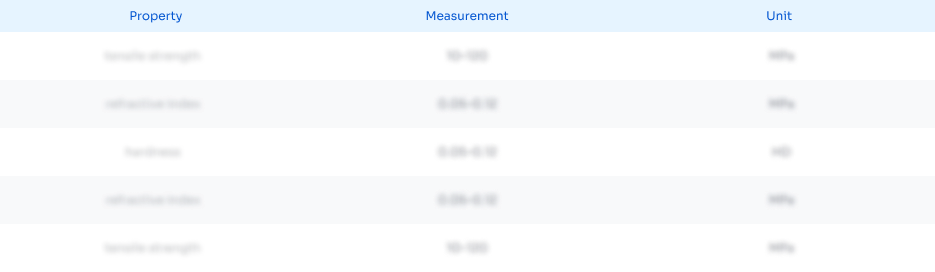
Abstract
Description
Claims
Application Information

- R&D
- Intellectual Property
- Life Sciences
- Materials
- Tech Scout
- Unparalleled Data Quality
- Higher Quality Content
- 60% Fewer Hallucinations
Browse by: Latest US Patents, China's latest patents, Technical Efficacy Thesaurus, Application Domain, Technology Topic, Popular Technical Reports.
© 2025 PatSnap. All rights reserved.Legal|Privacy policy|Modern Slavery Act Transparency Statement|Sitemap|About US| Contact US: help@patsnap.com