Machining method of glass preform
A processing method and glass technology, applied in glass forming, glass pressing, glass manufacturing equipment, etc., can solve the problems of glass bursting, complicated processing procedures, low yield of optical preforms, etc., and achieve good deformation performance
- Summary
- Abstract
- Description
- Claims
- Application Information
AI Technical Summary
Problems solved by technology
Method used
Image
Examples
Embodiment 1
[0071] Will As 40 Se 60 The chalcogenide glass clinker is added to the quartz crucible 111, so that the processing equipment is under vacuum or under the protection of the atmosphere; then the glass clinker is heated to 700°C to form a molten glass, and the molten glass is mechanically stirred during this period. Homogenization: after homogenization, the temperature of the molten glass is lowered to 360°C, so that the molten glass becomes a viscous glass, and the viscous glass is insulated.
[0072] Then heat the leaking tube 121 to melt the residual glass liquid in the leaking tube 121 and discharge it into the waste funnel.
[0073] Afterwards, pour the viscous liquid glass liquid into the leakage pipe 121, and inject the viscous liquid glass through the leakage pipe 121 into the forming mold of the leakage injection station 131; the weighing under the leakage injection station 131 After the device 136 weighs the forming mold to meet the standard, move the forming mold in ...
Embodiment 2
[0076] Will Ge 10 As 40 Se 50 The chalcogenide glass clinker is added to the quartz crucible 111, so that the processing equipment is under vacuum or under the protection of the atmosphere; then the glass clinker is heated to 700°C to form a molten glass, and the molten glass is mechanically stirred during this period. Homogenization: After homogenization, the temperature of the molten glass is lowered to 390°C, so that the molten glass becomes a viscous glass, and the viscous glass is kept warm until the temperature of the viscous glass is consistent.
[0077] Then heat the leaking tube 121 to melt the residual glass liquid in the leaking tube 121 and discharge it into the waste funnel.
[0078] Afterwards, pour the viscous liquid glass liquid into the leakage pipe 121, and inject the viscous liquid glass through the leakage pipe 121 into the forming mold of the leakage injection station 131; the weighing under the leakage injection station 131 After the device 136 weighs ...
Embodiment 3
[0081] Will Ge 33 As 12 Se 55 The chalcogenide glass clinker is added to the quartz crucible 111, so that the processing equipment is under vacuum or under the protection of the atmosphere; then the glass clinker is heated to 750°C to form a molten glass, and the molten glass is mechanically stirred during this period. Homogenization: after homogenization, the temperature of the molten glass is lowered to 500°C, so that the molten glass becomes a viscous glass, and the viscous glass is kept warm until the temperature of the viscous glass is consistent.
[0082] Then heat the leaking tube 121 to melt the residual glass liquid in the leaking tube 121 and discharge it into the waste funnel.
[0083]Afterwards, pour the viscous liquid glass liquid into the leakage pipe 121, and inject the viscous liquid glass through the leakage pipe 121 into the forming mold of the leakage injection station 131; the weighing under the leakage injection station 131 After the device 136 weighs t...
PUM
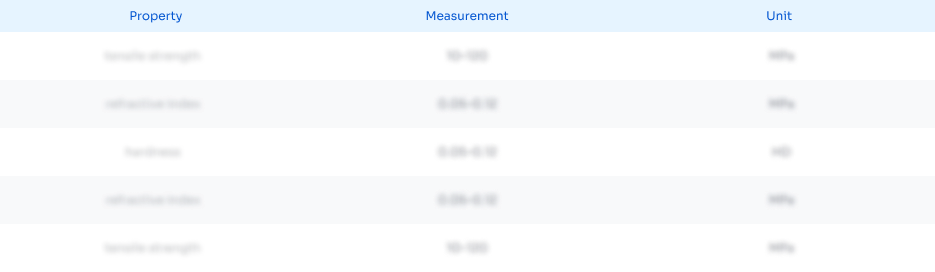
Abstract
Description
Claims
Application Information

- R&D
- Intellectual Property
- Life Sciences
- Materials
- Tech Scout
- Unparalleled Data Quality
- Higher Quality Content
- 60% Fewer Hallucinations
Browse by: Latest US Patents, China's latest patents, Technical Efficacy Thesaurus, Application Domain, Technology Topic, Popular Technical Reports.
© 2025 PatSnap. All rights reserved.Legal|Privacy policy|Modern Slavery Act Transparency Statement|Sitemap|About US| Contact US: help@patsnap.com