Full-automatic stamping system
A fully automatic, punching machine technology, applied in the field of machinery, can solve the problems of high risk factor, high cost of personnel consumption, and no blanking mechanism.
- Summary
- Abstract
- Description
- Claims
- Application Information
AI Technical Summary
Problems solved by technology
Method used
Image
Examples
Embodiment 1
[0021] Such as Figure 1-3 As shown, a fully automatic stamping system includes a load-bearing base 1, a delivery plate 2, a punching machine 3, a delivery slot 4 and a die slot 5, the top of the load-bearing base 1 is installed with a delivery plate 2 through a mounting frame, and the delivery plate 2 One side is provided with a punching machine 3 through a connecting frame, one side of the top of the punching machine 3 has a punching top die 6, and the other side of the delivery plate 2 is provided with a corresponding conveyor 14, and the two sides of the top of the conveyor 14 are installed by bolts. Switch 15, and the steel plate 16 is placed by the transmission belt between the infrared switches 15, the speed reduction motor 12 is installed on the top side of the delivery plate 2 through the mounting seat, and the movement plate 13 is installed on the side of the reduction motor 12 through the connecting rod. 2 The surface is provided with a drop slot 4 corresponding to ...
Embodiment 2
[0029] Such as Figure 1-3As shown, a fully automatic stamping system includes a load-bearing base 1, a delivery plate 2, a punching machine 3, a delivery slot 4 and a die slot 5, the top of the load-bearing base 1 is installed with a delivery plate 2 through a mounting frame, and the delivery plate 2 One side is provided with a punching machine 3 through a connecting frame, one side of the top of the punching machine 3 has a punching top die 6, and the other side of the delivery plate 2 is provided with a corresponding conveyor 14, and the two sides of the top of the conveyor 14 are installed by bolts. Switch 15, and the steel plate 16 is placed by the transmission belt between the infrared switches 15, the speed reduction motor 12 is installed on the top side of the delivery plate 2 through the mounting seat, and the movement plate 13 is installed on the side of the reduction motor 12 through the connecting rod. 2 The surface is provided with a drop slot 4 corresponding to t...
PUM
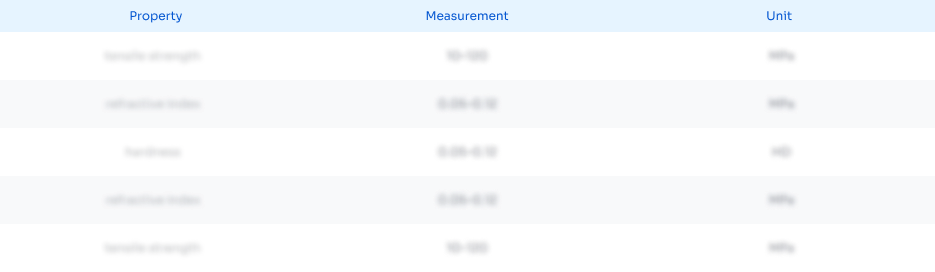
Abstract
Description
Claims
Application Information

- R&D Engineer
- R&D Manager
- IP Professional
- Industry Leading Data Capabilities
- Powerful AI technology
- Patent DNA Extraction
Browse by: Latest US Patents, China's latest patents, Technical Efficacy Thesaurus, Application Domain, Technology Topic, Popular Technical Reports.
© 2024 PatSnap. All rights reserved.Legal|Privacy policy|Modern Slavery Act Transparency Statement|Sitemap|About US| Contact US: help@patsnap.com