A kiln for the production of basalt fiber
A kiln and forming area technology, applied in the direction of manufacturing tools, glass manufacturing equipment, etc., can solve the problems of poor thermal conductivity, easy crystallization, high energy consumption, etc., and achieve the effects of ensuring product quality, reducing flow distance, and stabilizing the liquid level
- Summary
- Abstract
- Description
- Claims
- Application Information
AI Technical Summary
Problems solved by technology
Method used
Image
Examples
Embodiment 1
[0029] In this application, when the term bushing plate is used, it refers to all bushing plates including the first bushing plate and the second bushing plate.
[0030] refer to Figure 1-Figure 3 , along the first direction 100, the kiln for producing basalt fiber includes a feeder 1, a melting pool 2 and a molding area 3 connected in sequence. Both the feeding machine 1 and the forming area 3 are arranged on opposite sides of the melting pool 2 .
[0031] The melting pool 2 includes a shell 21 and a melting cavity 22 arranged in the shell. The top 25 of the casing 21 is provided with a second smoke exhaust port 26, and a second chimney 28 is installed on the second smoke exhaust port 26. For the convenience of controlling the amount of smoke exhaust, a second smoke exhaust port is provided with a The second adjusting plate 27, through which the size of the second smoke outlet can be adjusted, so as to adjust the amount of smoke exhausted. A row of second electric heaters...
Embodiment 2
[0049] This embodiment is an improvement on the basis of Embodiment 1. The main difference is that the installation positions of the first flame heater and the second flame heater are different. Please refer to Figure 5 , the second flame heater 61 is vertically installed on the top 25 of the shell, the first flame heater 62 is obliquely arranged on the top 35 of the molding area 3, and the flame injection direction 300 of the first flame heater 35 is aligned with the basalt in the main channel The angle α between the flow directions 200 of the melt is 45°. It can be understood that, in other embodiments, the included angle α may also be 30°, 40°, 50°, 100° or 150°, and of course it may also be any other angle between 30°-150°.
[0050] It can be understood that on the basis of Embodiment 1, only the position of the first flame heater or the second flame heater can be adjusted. Alternatively, a first flame heater is provided on the top of the molding area and on both side wa...
PUM
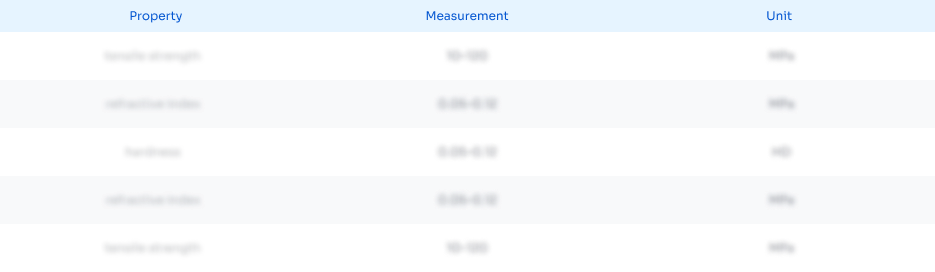
Abstract
Description
Claims
Application Information

- Generate Ideas
- Intellectual Property
- Life Sciences
- Materials
- Tech Scout
- Unparalleled Data Quality
- Higher Quality Content
- 60% Fewer Hallucinations
Browse by: Latest US Patents, China's latest patents, Technical Efficacy Thesaurus, Application Domain, Technology Topic, Popular Technical Reports.
© 2025 PatSnap. All rights reserved.Legal|Privacy policy|Modern Slavery Act Transparency Statement|Sitemap|About US| Contact US: help@patsnap.com