Numerical method for predicting pellet drying process in grate blast drying section
A drying process, blast drying technology, applied in calculation, electrical digital data processing, design optimization/simulation, etc., can solve problems such as ignoring moisture condensation, complex control equations, and inability to truly and accurately reflect the moisture transmission mechanism of pellets
- Summary
- Abstract
- Description
- Claims
- Application Information
AI Technical Summary
Problems solved by technology
Method used
Image
Examples
Embodiment Construction
[0174] The present invention will be further described below in conjunction with accompanying drawing.
[0175] The present invention first establishes the physical model of the pellet heat transfer drying process in the blast drying section of the grate machine, and on the basis of necessary simplified assumptions, establishes a mathematical model of the pellet heat transfer drying process, and finally obtains the pellets through actual tests. The temperature data of each layer of the material layer and the temperature data of each area in the grate are used to verify and adjust the established mathematical model, predict the drying process of the pellets in the blast drying section of the grate, and comprehensively analyze and optimize the control parameters and parameters in the actual drying process. Process parameters.
[0176]Most of the previous dry material layer models are mathematical models in the macroscopic sense. The heat transfer treatment in the model is relati...
PUM
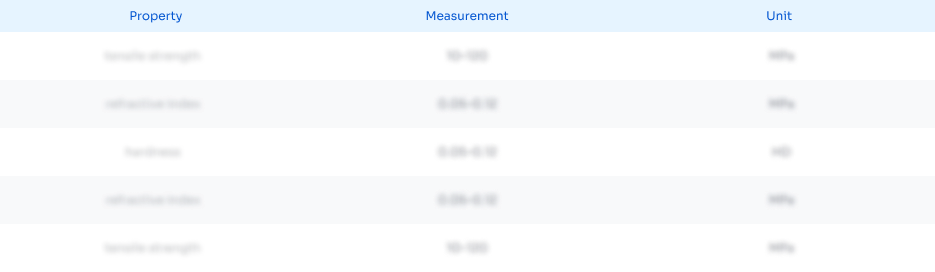
Abstract
Description
Claims
Application Information

- R&D
- Intellectual Property
- Life Sciences
- Materials
- Tech Scout
- Unparalleled Data Quality
- Higher Quality Content
- 60% Fewer Hallucinations
Browse by: Latest US Patents, China's latest patents, Technical Efficacy Thesaurus, Application Domain, Technology Topic, Popular Technical Reports.
© 2025 PatSnap. All rights reserved.Legal|Privacy policy|Modern Slavery Act Transparency Statement|Sitemap|About US| Contact US: help@patsnap.com