Rubber material for rubber shoe sole and preparation method thereof
A technology of rubber soles and rubber materials, applied in the direction of shoe soles, applications, footwear, etc., can solve the problems of poor compatibility, wear resistance and other performances that cannot meet actual needs, and achieve improved wear resistance, improved vulcanization effect, and enhanced The effect of abrasion resistance
- Summary
- Abstract
- Description
- Claims
- Application Information
AI Technical Summary
Problems solved by technology
Method used
Image
Examples
Embodiment 1
[0031] The sizing material for rubber soles of the present embodiment is made of the following raw materials in parts by weight: 45 parts of nitrile rubber, 35 parts of silicone rubber, 5 parts of rubber-plastic alloy, 4 parts of modified vinyl resin, modified rare earth oxide 3 parts of compound, 1 part of vulcanizing agent, 3 parts of dipentamethylene thiuram tetrasulfide, 2 parts of dicumyl peroxide, 4 parts of maleic anhydride grafted polyethylene, 2 parts of zinc methacrylate, o-phthalic acid 5 parts of dibutyl diformate, 3 parts of pentaerythritol stearate, 10 parts of modified nano wear-resistant filler, 3 parts of zinc ricinoleate, 2 parts of activator, 1 part of softener, 0.5 parts of rubber accelerator, anti-aging agent 0.4 parts.
[0032] Wherein, the rubber-plastic alloy is formed by high-temperature blending of powdered nitrile rubber and PBT at a weight ratio of 3:1.
[0033]Wherein, the preparation method of the modified vinyl resin comprises: putting the vinyl...
Embodiment 2
[0048] The sizing material for rubber soles of the present embodiment is made of the following raw materials in parts by weight: 65 parts of nitrile rubber, 45 parts of silicone rubber, 10 parts of rubber-plastic alloy, 8 parts of modified vinyl resin, modified rare earth oxide 6 parts of compound, 4 parts of vulcanizing agent, 7 parts of dipentamethylene thiuram tetrasulfide, 6 parts of dicumyl peroxide, 8 parts of maleic anhydride grafted polyethylene, 4 parts of zinc methacrylate, o-phthalic acid 10 parts of dibutyl diformate, 6 parts of pentaerythritol stearate, 20 parts of modified nano wear-resistant filler, 7 parts of zinc ricinoleate, 5 parts of activator, 3 parts of softener, 1.5 parts of rubber accelerator, anti-aging agent 0.8 servings.
[0049] Wherein, the rubber-plastic alloy is formed by high-temperature blending of powdered nitrile rubber and PBT at a weight ratio of 3:1.
[0050] Wherein, the preparation method of the modified vinyl resin comprises: putting t...
Embodiment 3
[0065] The sizing material for rubber soles of the present embodiment is made of the following raw materials in parts by weight: 55 parts of nitrile rubber, 40 parts of silicone rubber, 7.5 parts of rubber-plastic alloy, 6 parts of modified vinyl resin, modified rare earth oxide 4.5 parts of compound, 2.5 parts of vulcanizing agent, 5 parts of dipentamethylene thiuram tetrasulfide, 4 parts of dicumyl peroxide, 6 parts of maleic anhydride grafted polyethylene, 3 parts of zinc methacrylate, o-phthalic acid 7.5 parts of dibutyl diformate, 4.5 parts of pentaerythritol stearate, 15 parts of modified nano wear-resistant filler, 5 parts of zinc ricinoleate, 3.5 parts of activator, 2 parts of softener, 1 part of rubber accelerator, anti-aging agent 0.6 parts.
[0066] Wherein, the rubber-plastic alloy is formed by high-temperature blending of powdered nitrile rubber and PBT at a weight ratio of 3:1.
[0067] Wherein, the preparation method of the modified vinyl resin comprises: putti...
PUM
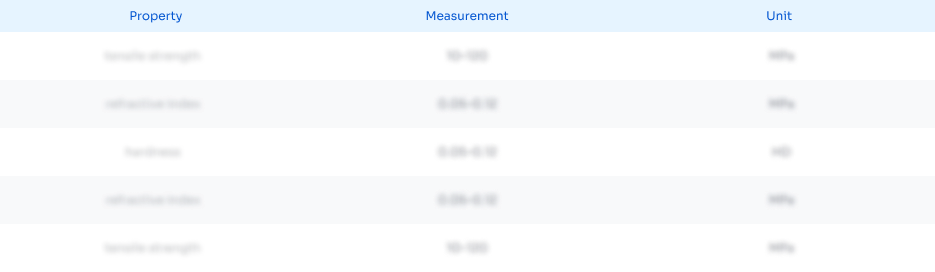
Abstract
Description
Claims
Application Information

- R&D
- Intellectual Property
- Life Sciences
- Materials
- Tech Scout
- Unparalleled Data Quality
- Higher Quality Content
- 60% Fewer Hallucinations
Browse by: Latest US Patents, China's latest patents, Technical Efficacy Thesaurus, Application Domain, Technology Topic, Popular Technical Reports.
© 2025 PatSnap. All rights reserved.Legal|Privacy policy|Modern Slavery Act Transparency Statement|Sitemap|About US| Contact US: help@patsnap.com