Preparation method of fine-sand-shaped raw material
A raw material and fine sand technology, applied in the field of additive manufacturing, can solve the problems of fine sand-like raw material configuration and unstable mixing uniformity, and achieve the effects of avoiding product quality defects, improving automation, and improving performance
- Summary
- Abstract
- Description
- Claims
- Application Information
AI Technical Summary
Problems solved by technology
Method used
Image
Examples
Embodiment 1
[0038] Example 1: The fine sand-like raw material is only new silica sand
[0039] The configuration and mixing method of the fine sandy raw material used for the production of said process vase are as follows:
[0040] In the first step, enter the new sand standard sand volume of 240kg on the control panel of the additive manufacturing equipment, and enter the configuration volume of the curing agent 2.52L;
[0041] The second step is to read the actual amount of silica sand in the sand-adding funnel. If the actual amount of silica sand in the sand-adding funnel is not less than the minimum amount of sand, then do not add new silica sand to the sand-adding funnel. If the amount of silica sand in the sand-adding funnel If the actual amount of sand is less than the minimum amount of sand, execute the "third step";
[0042] The third step is to detect the state of the sand outlet butterfly valve of the sand adding funnel. If the sand outlet butterfly valve of the sand adding fu...
Embodiment 2
[0057] Embodiment two: the raw material of fine sand is new silica sand and old silica sand
[0058] In this embodiment, the sand adding funnel is divided into a new sand adding sand funnel and an old sand adding sand funnel, and the sand outlets of both are connected with the sand mixing tank, and the ratio of new silica sand to old silica sand is 7:3, according to If the total silica sand required is 240kg, then the new silica sand is 168kg, the old silica sand is 72kg, and only the new sand needs to be equipped with a curing agent, so the required curing agent is 1.76L.
[0059] In the first step, input the standard sand volume of new silica sand 168kg, the standard sand volume of old silica sand 72lg on the control panel of the additive manufacturing equipment, and input the configuration volume of curing agent 1.76L;
[0060] The second step is to read the actual amount of silica sand in the new sand-adding funnel. If the actual amount of silica sand in the new-sand-addin...
PUM
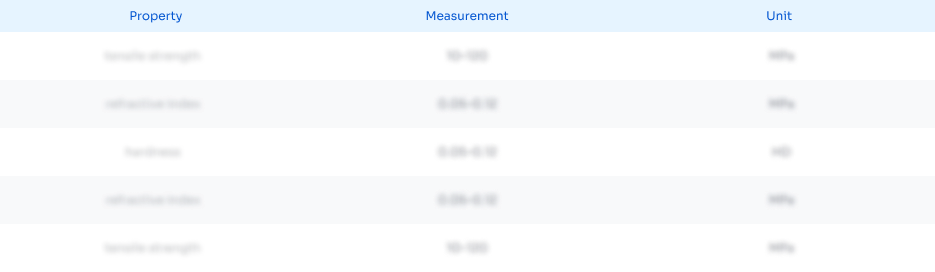
Abstract
Description
Claims
Application Information

- R&D
- Intellectual Property
- Life Sciences
- Materials
- Tech Scout
- Unparalleled Data Quality
- Higher Quality Content
- 60% Fewer Hallucinations
Browse by: Latest US Patents, China's latest patents, Technical Efficacy Thesaurus, Application Domain, Technology Topic, Popular Technical Reports.
© 2025 PatSnap. All rights reserved.Legal|Privacy policy|Modern Slavery Act Transparency Statement|Sitemap|About US| Contact US: help@patsnap.com