Method for predicting the wear life of stamping dies with full-time wear accumulation
A stamping die and wear life technology, applied in the field of die stamping, can solve the problems of ignoring the influence of contact stress and slip speed, low prediction accuracy, etc., to reduce the complexity of the problem and improve the efficiency.
- Summary
- Abstract
- Description
- Claims
- Application Information
AI Technical Summary
Problems solved by technology
Method used
Image
Examples
Embodiment 1
[0044] The invention provides a method for predicting the wear life of a stamping die with full-time wear accumulation, and its implementation process is as follows figure 1 shown, including the following steps:
[0045] Step S101, taking mold materials with different surface treatments, such as mold materials that undergo electrochrome plating after laser quenching (herein referred to as the first mold material) and mold materials that have only undergone laser quenching heat treatment (herein referred to as the first mold material) as the second mold material).
[0046] Step S102, using a wear testing machine to measure the wear coefficient (indicated by K), roughness coefficient (indicated by R), specific gravity α of adhesive wear and specific gravity β of abrasive wear of the first mold material and the second mold material respectively.
[0047] Step S103, conducting electrochrome plating experiment and laser quenching finite element simulation experiment on the first m...
example
[0074] Taking the die used for punching the outer panel of the engine cover of an automobile (referred to as the outer panel die of the engine cover in this article) as an example, the prediction method proposed in this patent is used to predict the wear life of the outer panel die of the engine cover. The specific implementation method is as follows :
[0075] 1) Through the electrochrome plating experiment and laser quenching simulation of the engine cover outer plate mold material, the relationship between the hardness and wear depth of the engine cover outer plate mold material in the process of laser quenching and electrochrome plating treatment is obtained , it can be seen that the hardness of the engine cover outer plate mold material shows a gradient trend as the wear depth gradually increases from the outermost surface to the core.
[0076] The relationship between the Brinell hardness of the engine cover outer plate mold and the wear depth is expressed by the followi...
PUM
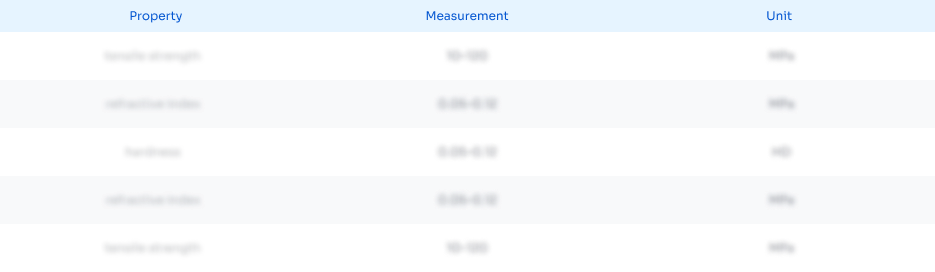
Abstract
Description
Claims
Application Information

- R&D Engineer
- R&D Manager
- IP Professional
- Industry Leading Data Capabilities
- Powerful AI technology
- Patent DNA Extraction
Browse by: Latest US Patents, China's latest patents, Technical Efficacy Thesaurus, Application Domain, Technology Topic, Popular Technical Reports.
© 2024 PatSnap. All rights reserved.Legal|Privacy policy|Modern Slavery Act Transparency Statement|Sitemap|About US| Contact US: help@patsnap.com