Preparation process of magnesium alloy wet-and-heat-resistant conductive-anti-corrosion chemical conversion film
A technology of chemical conversion film and preparation process, which is applied in the field of chemical conversion process, which can solve the problems of limited number of conductive-corrosion film layers, small coverage, and inability to meet the application requirements of actual components, so as to achieve uniform and smooth surface of the film layer and easy operation Simple and low-cost effect
- Summary
- Abstract
- Description
- Claims
- Application Information
AI Technical Summary
Problems solved by technology
Method used
Image
Examples
Embodiment 1
[0032] The preparation method is as follows: the sample is cast AZ91D magnesium alloy;
[0033] 1. Grinding pretreatment: Grinding with sandpaper to remove burrs, firm oxides, release agents, casting sand, cutting oil and other foreign matter to reduce surface roughness.
[0034] 2. Pre-pickling treatment: immerse the polished sample in a sulfuric acid pickling solution with a concentration of 2ml / L at a temperature of 30°C. The etching treatment time is 5 minutes. Take out the processed sample and use a deionized Wash with water 3 times until the residual sulfuric acid solution on the surface is removed. In an acidic environment, the β second phase and the α base phase in the AZ91D magnesium alloy form a height difference of 5-10 μm due to severe galvanic corrosion, which is the Mg(OH) formed by the α base phase in the damp heat test. 2 Corrosion products reserve growth space, so that the height of the β second phase is higher than that of the α base phase after the damp hea...
Embodiment 2
[0039] The preparation method is as follows: the sample is cast AZ91D magnesium alloy;
[0040] 1. Grinding pretreatment: Grinding with sandpaper to remove burrs, firm oxides, release agents, casting sand, cutting oil and other foreign matter to reduce surface roughness.
[0041] 2. Pre-pickling treatment: immerse the polished sample in a sulfuric acid pickling solution with a concentration of 1ml / L at a temperature of 30°C. The etching treatment time is 1min. Take out the processed sample and use a deionized Wash with water 3 times until the residual sulfuric acid solution on the surface is removed. In an acidic environment, the β second phase and the α base phase in the AZ91D magnesium alloy form a height difference of 5-10 μm due to severe galvanic corrosion, which is the Mg(OH) formed by the α base phase in the damp heat test. 2 Corrosion products reserve growth space, so that the height of the β second phase is higher than that of the α base phase after the damp heat tes...
Embodiment 3
[0046] The preparation method is as follows: the sample is cast AZ91D magnesium alloy;
[0047] 1. Grinding pretreatment: Grinding with sandpaper to remove burrs, firm oxides, release agents, casting sand, cutting oil and other foreign matter to reduce surface roughness.
[0048] 2. Pickling pretreatment: immerse the polished sample in a sulfuric acid pickling solution with a concentration of 10ml / L at a temperature of 50°C. The etching treatment time is 20 minutes. Take out the processed sample and use a deionized Wash with water 3 times until the residual sulfuric acid solution on the surface is removed. In an acidic environment, the β second phase and the α base phase in the AZ91D magnesium alloy form a height difference of 5-10 μm due to severe galvanic corrosion, which is the Mg(OH) formed by the α base phase in the damp heat test. 2 Corrosion products reserve growth space, so that the height of the β second phase is higher than that of the α base phase after the damp he...
PUM
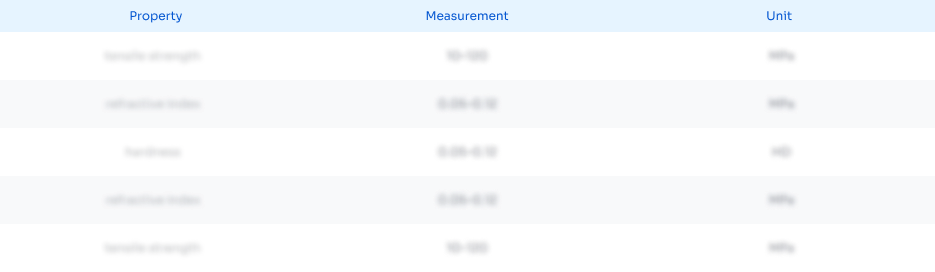
Abstract
Description
Claims
Application Information

- R&D Engineer
- R&D Manager
- IP Professional
- Industry Leading Data Capabilities
- Powerful AI technology
- Patent DNA Extraction
Browse by: Latest US Patents, China's latest patents, Technical Efficacy Thesaurus, Application Domain, Technology Topic, Popular Technical Reports.
© 2024 PatSnap. All rights reserved.Legal|Privacy policy|Modern Slavery Act Transparency Statement|Sitemap|About US| Contact US: help@patsnap.com