Continuous catalytic reforming method capable of achieving upflow regeneration of catalyst and adsorption and recovery of chlorine in coke-burning gas
A reforming catalyst and countercurrent regeneration technology, which is applied in the control/regulation of reforming operation, catalytic reforming of naphtha, etc., can solve the problems such as the decrease of the specific surface area of the catalyst, the impact on the long-term operation of the device, and the lack of adjustment means, etc., to achieve Reduce the loss of specific surface area, prolong the service life, ensure the effect of activity and selectivity
- Summary
- Abstract
- Description
- Claims
- Application Information
AI Technical Summary
Problems solved by technology
Method used
Image
Examples
Embodiment 1
[0029] A method for continuous reforming catalyst countercurrent regeneration and adsorption recovery of chlorine in coke gas, the process flow is as follows figure 1 As shown, the following steps are taken:
[0030] 1) The raw catalyst from the bottom of the reactor is cooled to 138°C and lifted into the raw catalyst separation hopper 4, and the catalyst fragments and powder carried in the catalyst are elutriated;
[0031] 2) The standby catalyst coming out of the standby catalyst separation hopper 4 enters the chlorine adsorption tank 3 to contact with the charred gas to absorb chlorine and hydrogen chloride in the charred gas, and a dechlorination tank 10 is also arranged behind the chlorine adsorption tank 3;
[0032] 3) The standby catalyst that has adsorbed chlorine and hydrogen chloride in the burnt gas is boosted to 0.50 MPa through the lock hopper 2 and then enters the regenerator 1;
[0033] 4) The regenerator 1 includes an upper coking section A and a lower coking ...
Embodiment 2
[0042] A method for countercurrent regeneration of a continuous reforming catalyst and adsorption recovery of chlorine in coke gas, the following steps are used:
[0043] 1) The raw catalyst from the bottom of the final reactor is cooled to 150°C and lifted into the raw catalyst separation hopper, and the catalyst fragments and powder carried in the catalyst are elutriated;
[0044] 2) The standby catalyst coming out of the standby catalyst separation hopper enters the chlorine adsorption tank to contact with the charred gas, and absorb the chlorine and hydrogen chloride in the charred gas;
[0045] 3) The standby catalyst that has adsorbed chlorine and hydrogen chloride in the coke gas is boosted to 0.65MPa through the lock hopper and then enters the regenerator;
[0046] 4) The regenerator includes an upper coking section and a lower coking section; the raw catalyst first enters the upper coking section, contacts with secondary coking gas at 500°C and contains 0.5v% oxygen, ...
PUM
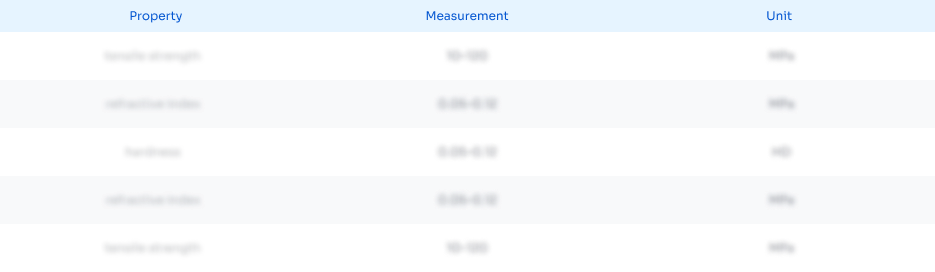
Abstract
Description
Claims
Application Information

- R&D
- Intellectual Property
- Life Sciences
- Materials
- Tech Scout
- Unparalleled Data Quality
- Higher Quality Content
- 60% Fewer Hallucinations
Browse by: Latest US Patents, China's latest patents, Technical Efficacy Thesaurus, Application Domain, Technology Topic, Popular Technical Reports.
© 2025 PatSnap. All rights reserved.Legal|Privacy policy|Modern Slavery Act Transparency Statement|Sitemap|About US| Contact US: help@patsnap.com